Tin plating involves an electrolytic process. Specifically designed tanks house items to be coated, serving as cathodes (negatively charged electrodes). At the edge of the tank stands an anode (positively charged electrode).
Tin coating provides good solderability and corrosion durability, yet can form long metal threads known as whiskers that cause current division or short circuiting issues in electronic components.
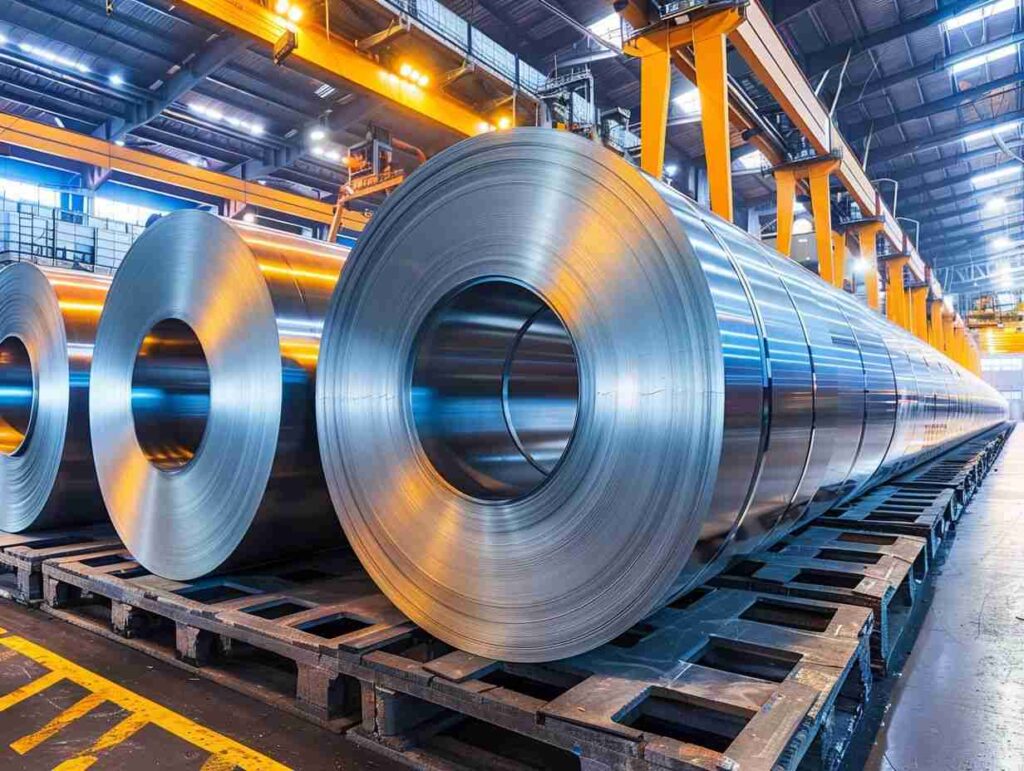
What causes oxidation?
Tin plating is a process in which a thin coating of tin is applied over a substrate to protect and improve its aesthetic appeal. This technique can be applied to ferrous and non-ferrous metals alike for corrosion or oxidation protection or simply creating an attractive appearance.
Electroplating is typically used to apply tin plate coating. This process entails passing an electric current through an aqueous solution of tin chemistry and applying positive electrical charge at one electrode to cause its molecules to attract onto metal parts in the substrate; then switching on negatively charged cathode electrode to complete plating cycle.
EC Williams provides a full selection of electroplating services tailored specifically to meet the needs of its customers. We will work with you to select the appropriate process, while offering top-quality coating that protects against oxidation of substrate surfaces.
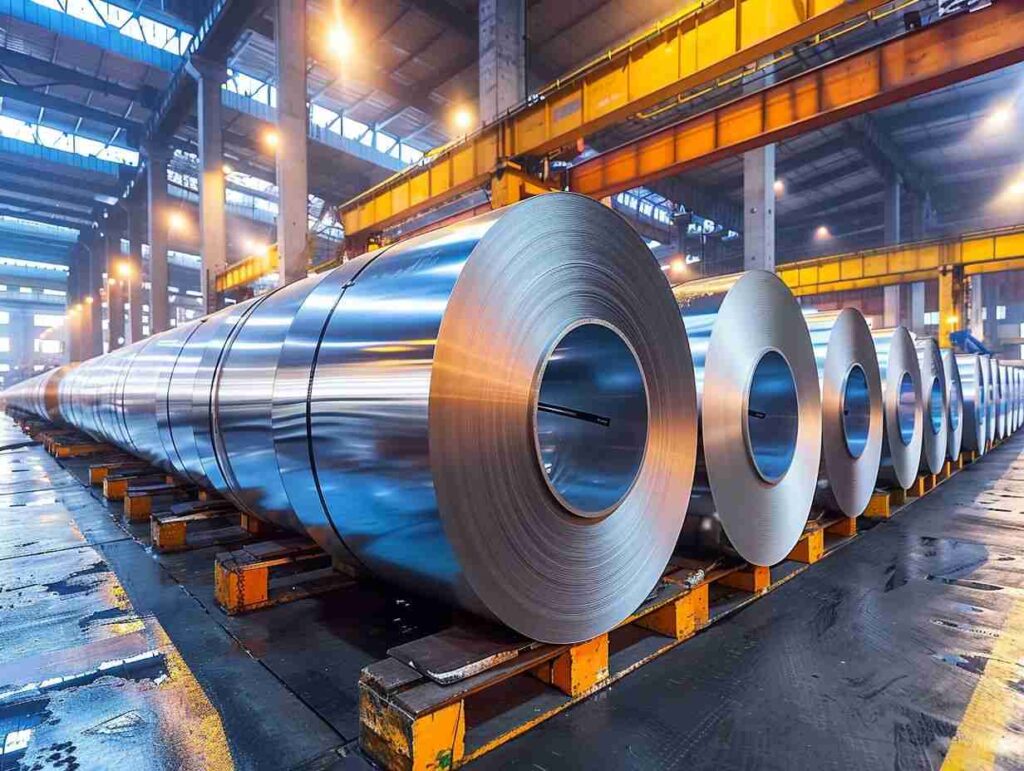
Tin electroplating is an efficient and cost-effective method for protecting metal surfaces from corrosion or oxidation, including copper, that are susceptible to rust or oxidation. Tin can also be used to coat components designed for soldering or electric contact solder points.
One of the primary factors contributing to tin oxidation is impurities present in tin plating solutions, typically caused by inferior additives or impurity ions from other metals in the plating solution. Impurities disrupt normal deposition processes for depositing tin coating and lead to yellowing over time.
Tin oxidation can also occur from improper storage and handling of the product plated with it. It’s essential that tin-plated items be stored in an environment with ample airflow in order to minimize rapid tin oxidization that would leave a thick gray layer covering that must be cleared away before soldering or other uses for them can begin.
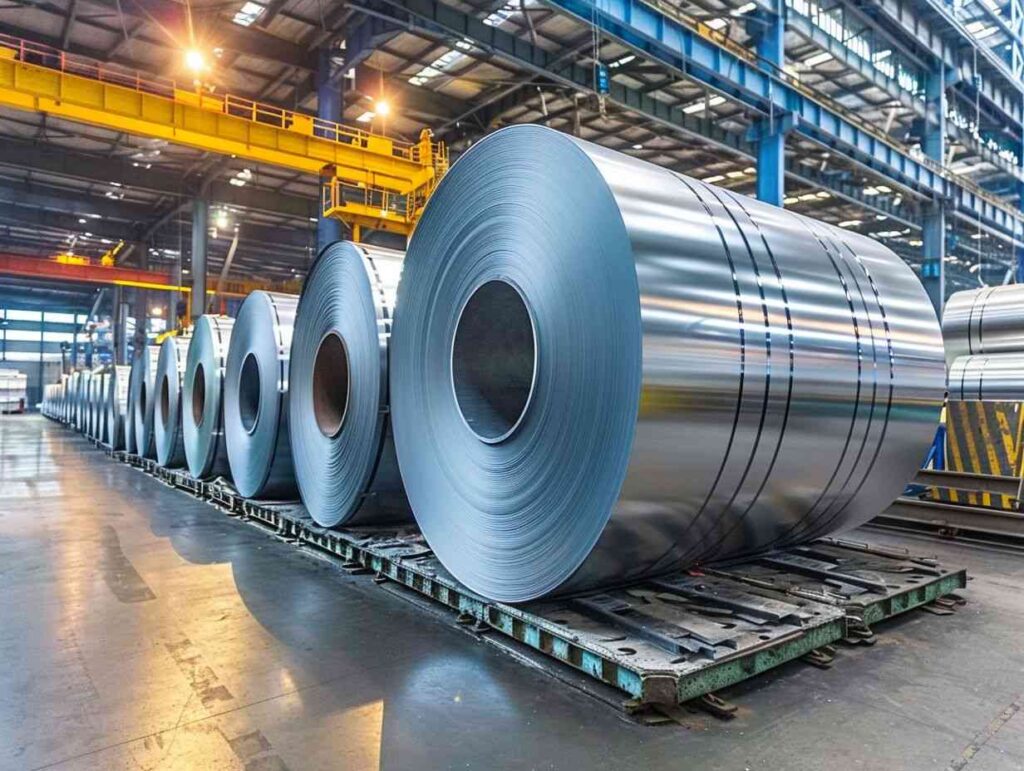
Where does oxidation occur?
Tin plating produces a white silvery deposit with corrosion-resistance and solderability characteristics, making it suitable for electrical contacts, switchgear, and industrial equipment. Tin plating also boasts hypoallergenic qualities that make it safe to be in direct contact with food products; making tin an appealing option for surfaces which will come into contact with food or beverages such as table tops.
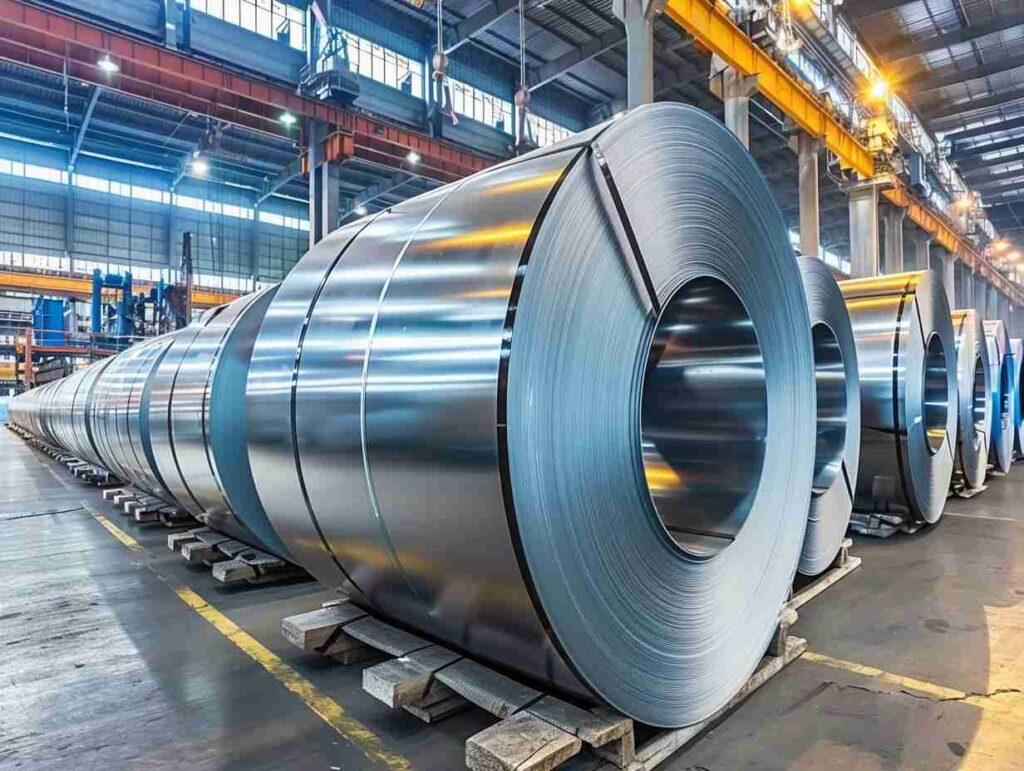
After depositing, tin can be polished to eliminate any imperfections or rough areas and apply a clear lacquer as soon as it cools to protect against corrosion and oxidation.
If an item requires higher conductivity levels, tin may be combined with lead to create tin/lead plate for increased corrosion resistance and solderability while still offering good conductivity levels. This combination offers superior corrosion protection while still offering good conductivity levels.
Tin/lead can also be plated over copper for corrosion resistant applications that require durability and corrosion resistance, making it an economical alternative to gold in terms of price and corrosion resistance. However, please keep in mind that tin/lead will oxidize faster than pure tin.
Tin plating’s main drawback lies in the formation of “Tin Whiskers,” or micro metal fibers that proliferate after exposure to air. While cosmetically undesirable, these whiskers present an imminent safety risk for electronic components as their conductivity could short-circuit components and lead to their failure.
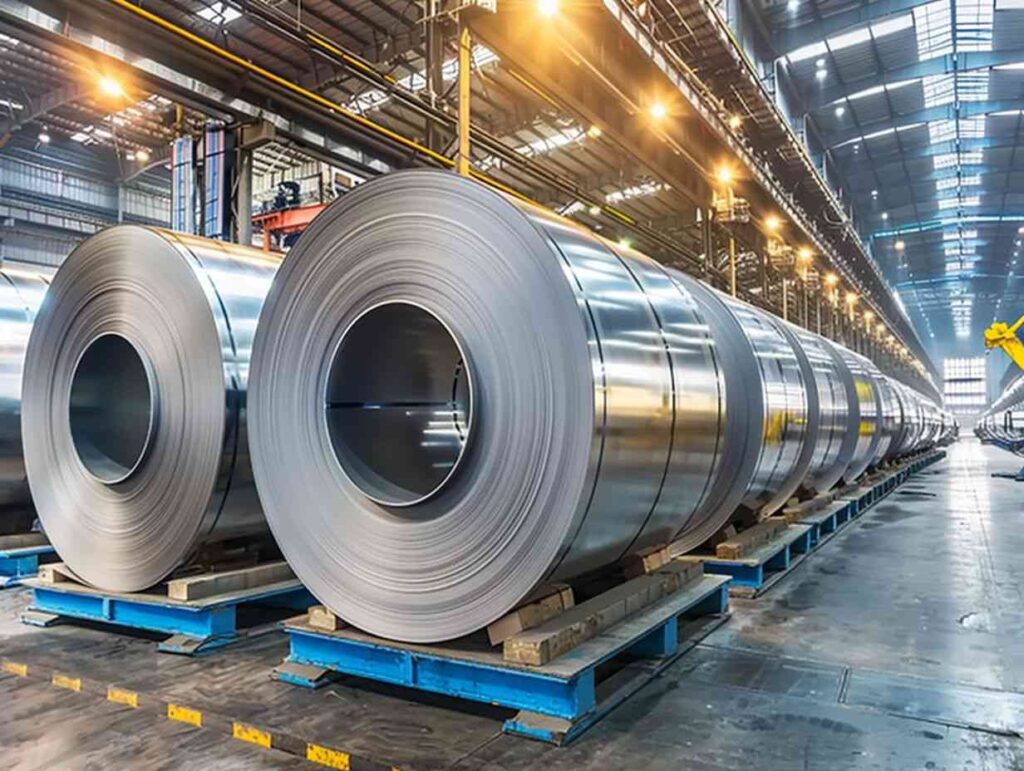
How does tin oxidize?
Tin is one of the most widely-used metals across various industries, due primarily to its impressive solderability and corrosion protection properties. One common method for coating objects with tin is electroplating; this involves coating them using electricity to attract tin ions onto an object’s surface for coating purposes – an economical, swift, and effective process that gives lasting results.
Before electroplating tin onto a substrate, it must first be thoroughly cleaned using grit blasting, where an electric current passes through a mixture of crushed glass, aluminum oxide, steel wool, corn cobs or walnut shells under pressure – this removes grease and oil that accumulates on its surface and allows electroplating to take place successfully.
After placing the substrate into an electrolytic solution called a plating bath, which consists of a tank containing one or more tin salts dissolved in water, its contents must then be charged with an electric current using a device called a rectifier to convert AC into DC current and charge both anode and cathode with electricity – once this process occurs positively charged anode ions will move towards negatively charged cathodes (substrates) via electrolyte bath to deposit tin onto them.
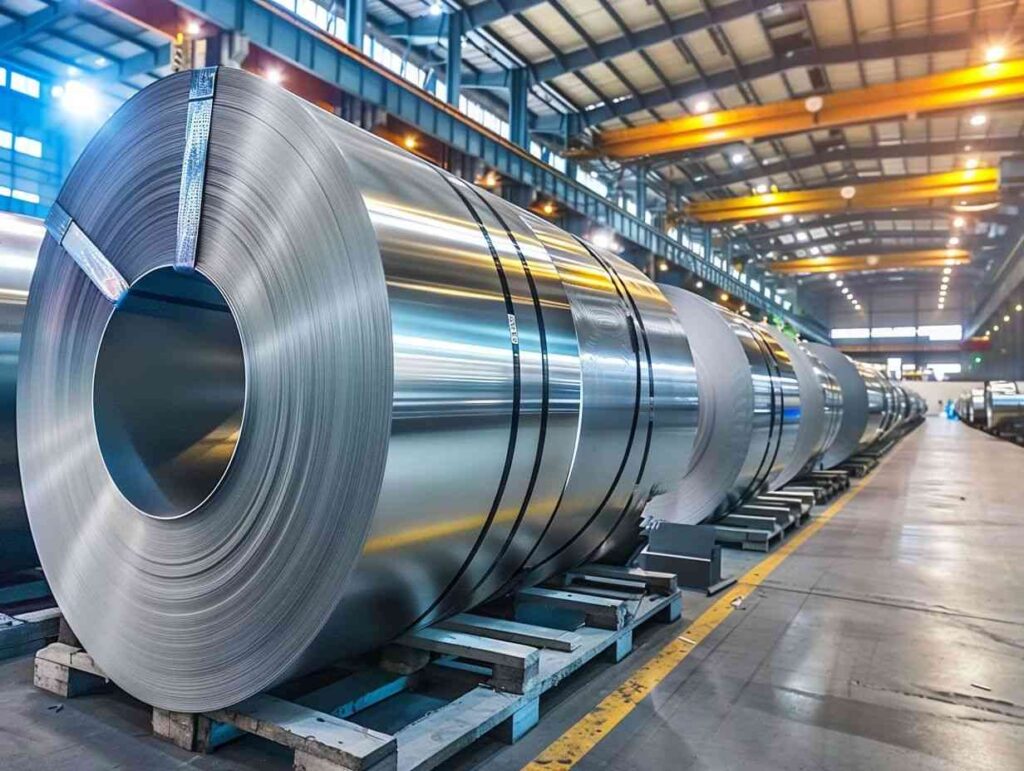
Once tin has been applied, it must be thoroughly rinsed off in order to eliminate any excess. Doing this also ensures a strong bond with its substrate material – essential if hydrogen embrittlement occurs due to incomplete bonding of tin with base materials.
Passivation can help increase corrosion protection characteristics and retard the oxidation process in tin plates, prolonging solderability while simultaneously increasing corrosion resistance. After being passivated, solderability will improve as will corrosion resistance levels.
What can be done to prevent oxidation?
There are a few steps that can help ensure that tin plating remains resistant to oxidation. First, ensure your substrate is free from contaminants before starting electroplating process. Second, lower current density during pre-plating stage to protect from corrosion and oxidization; lastly use Techni Eco Antioxidant as an antioxidant solution to slow rate at which tin oxidizes.
These steps will extend the lifespan of your tin plating. However, for more permanent solutions you could try investing in a low melting point that can withstand higher temperatures tin coating which offers excellent resistance against oxidation and corrosion to increase its lifespan and extend its lifespan.
Tin is widely utilized in electronics applications. As an economical yet robust material that provides corrosion and erosion protection compared to copper and other metals, tin conforms with RoHS regulations for safe usage in multiple environments.
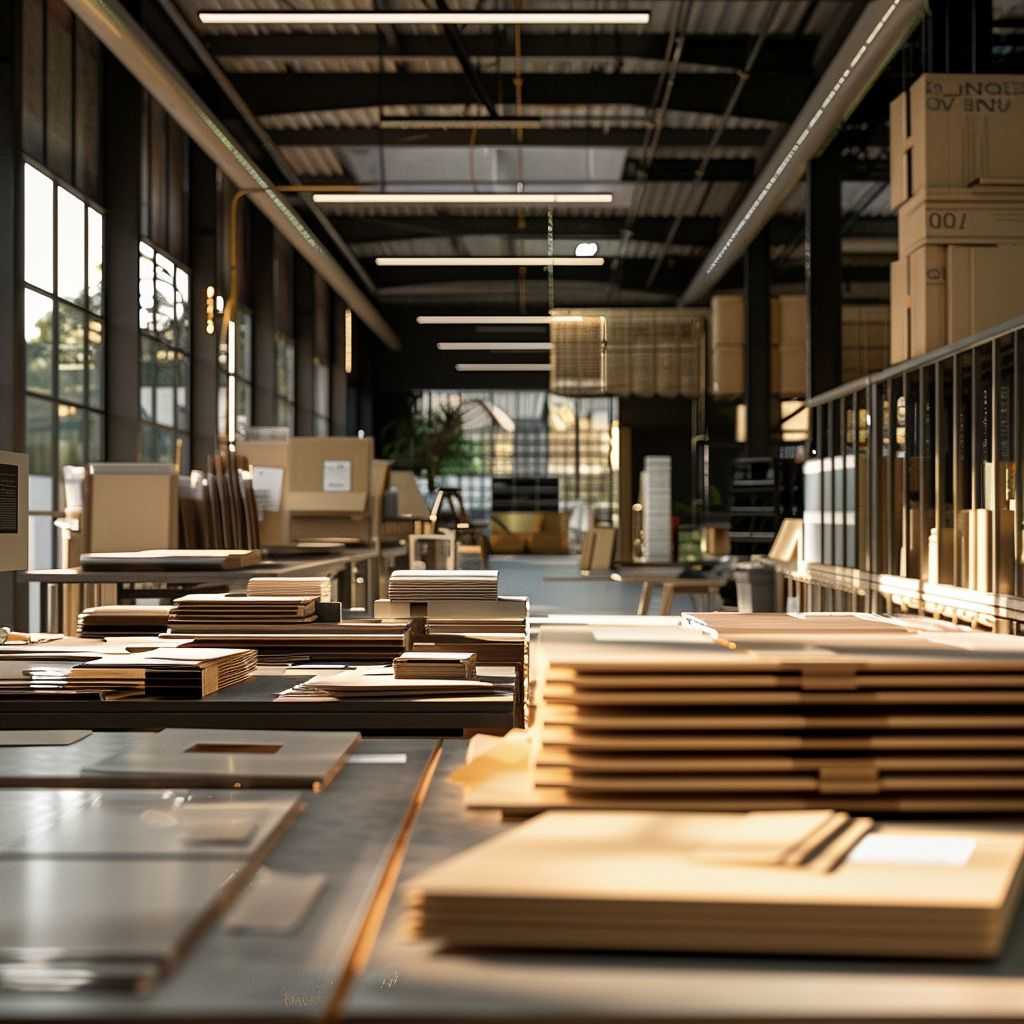
Tin does have some weaknesses that can be exploited in certain applications, most notably tin whiskers and dendritic crystal growths (dendrites). Both phenomena can cause short circuits, critical disruptions to electronic devices, as well as other issues. They may arise due to poor chemistry, underplating or improper reflow processes – three possible sources.
To reduce risk and ensure optimal results, we suggest using either a nickel under-plate or co-deposit with tin as an underlayer, and/or applying matte tin deposits that have low luminescent appearances. Also ensure to bake parts before plating to lower hydrogen concentrations and prevent intermetallic migration.