Silver has long been used in multiple industries, from healthcare and consumer to electronics, automotive and power generation. Due to its antibacterial properties, it has long been popular within healthcare settings.
Silver’s non-tarnish properties make it the perfect plating choice for low voltage signal transmission applications where even minor variations in contact resistance may have an impactful impact on product performance.
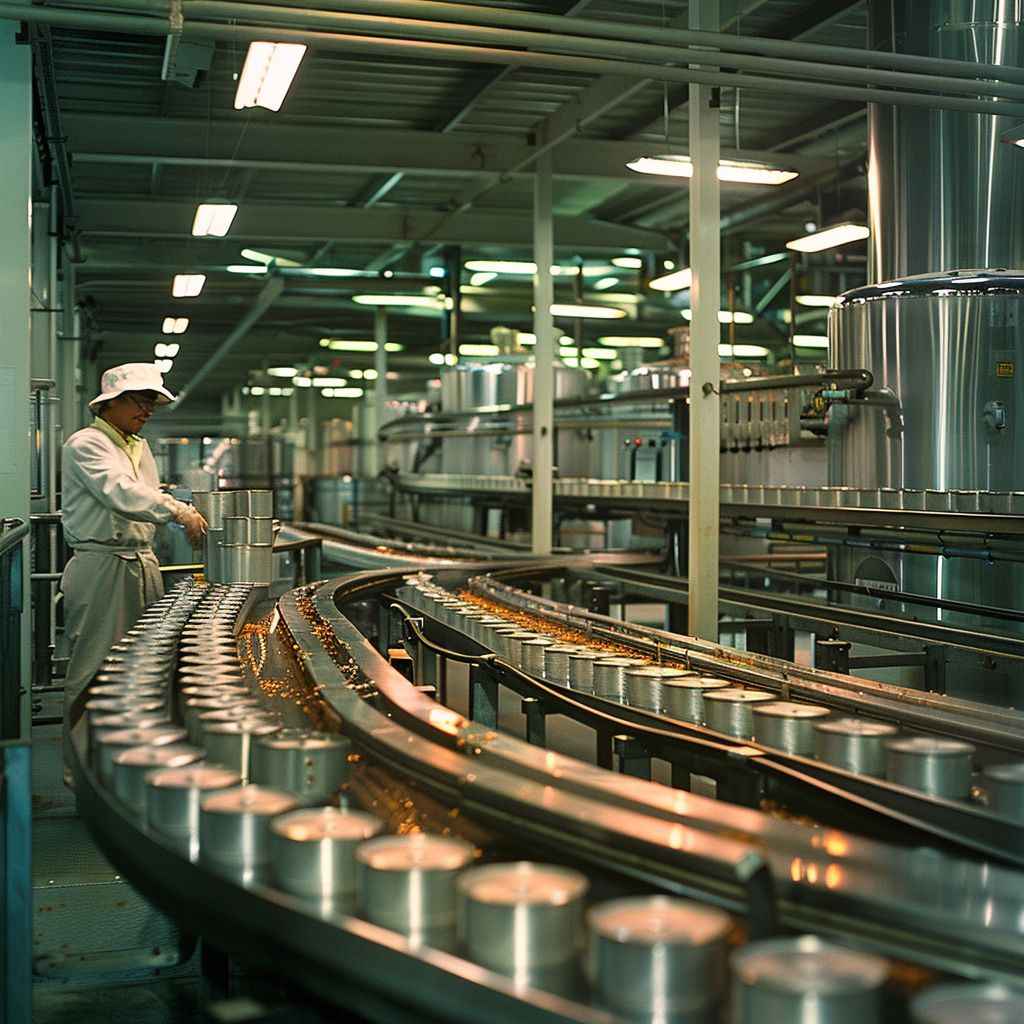
Cost
Silver plating can be more costly than its less-expensive counterparts like tin plating but less so than gold and platinum plating; nonetheless, it remains more cost-effective for industrial applications than using these more precious precious metals.
Due to its excellent solderability, conductivity, corrosion resistance and beautiful lustrous finish it makes a popular choice in multiple industries and applications – typically consumer electronics, jewelry and telecommunications; it may also be utilized by manufacturers of larger electrical components.
Although silver plating offers many advantages, there are certain key considerations when selecting a type for your project. For instance, thickness can impact corrosion resistance and solderability; thicker layers offer better results while thinner ones may be prone to oxidation or adherance issues on different substrates. Furthermore, coatings are sensitive to temperature and humidity fluctuations so finding an experienced supplier who understands your unique product requirements is also key.
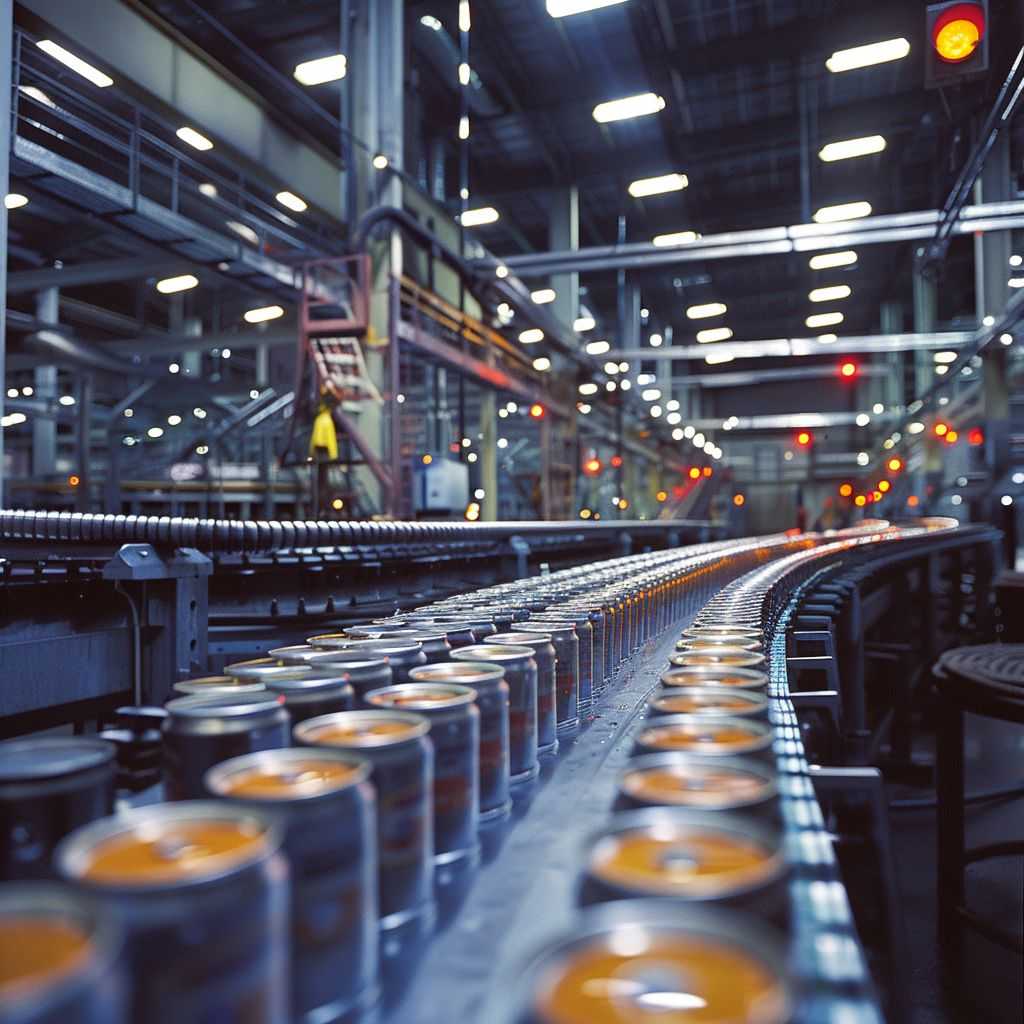
Tin plating presents another issue when it comes to creating whiskers – microscopic metal filaments that can pose serious danger in high voltage environments and cause short circuits, current arcs and critical disruption. To avoid whiskers altogether it is recommended that either nickel underplating is utilized or the tin is co-deposited with at least 2% lead to co-deposit it with sufficient thickness to obviate this issue.
Your best option when it comes to silver plating is working with an experienced supplier who can develop a tailored process tailored to your specifications, producing top-quality results. In addition, these suppliers may provide useful tips to prevent your coating from tarnishing or losing its shine; such as using non-sulfur bearing plastic bags, desiccates or silver saver paper storage solutions.
Valence Plating can provide exceptional plating services, offering military-spec finishes compliant with RoHS and FDA standards and FDA regulations on an array of products. We’ll work closely with you to select the appropriate metal for your application while guaranteeing an impeccable finish, providing outstanding customer service in turn.
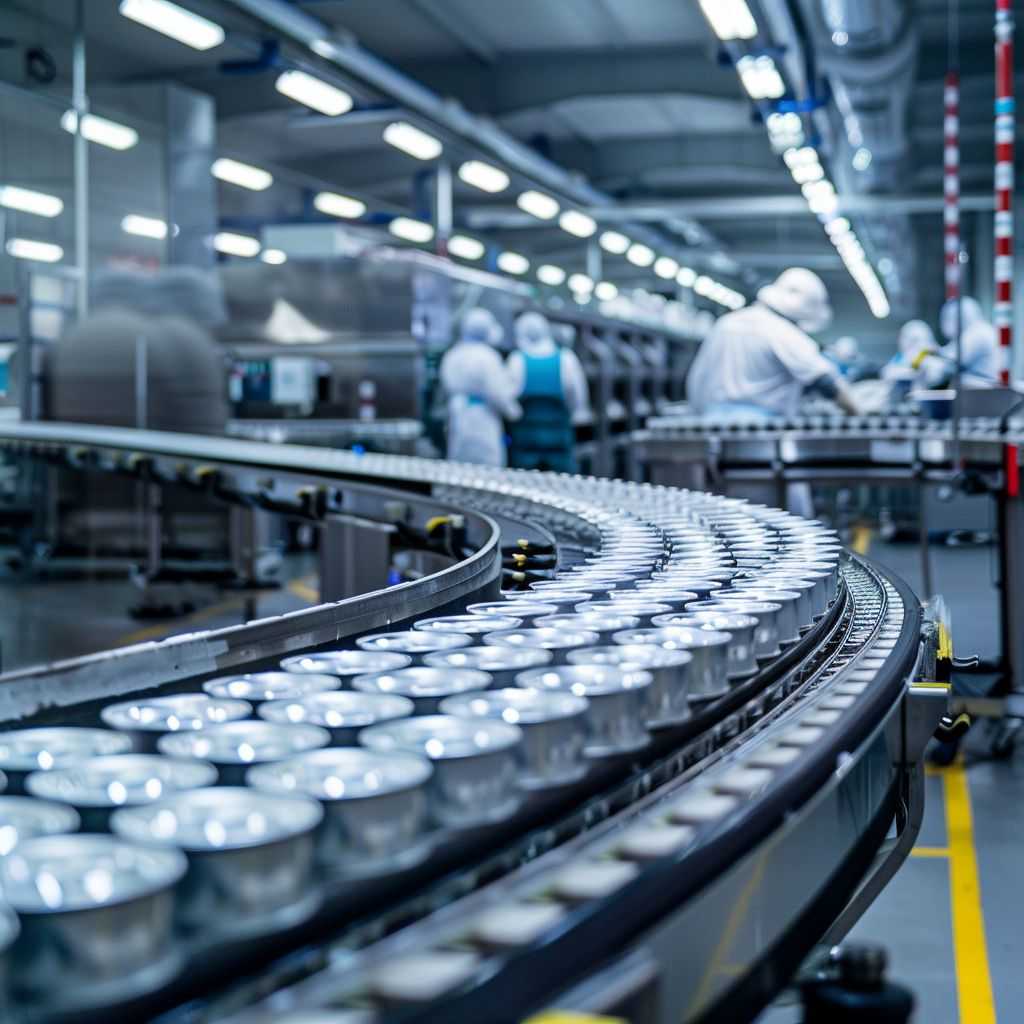
Corrosion Resistance
Silver is an exceptional metal when it comes to corrosion resistance. Industrial silver plating can be used to increase this protection in copper, aluminum and other degrading metals – making it the ideal choice for electronics, aerospace and automotive industries. Silver also provides outstanding lubricity which reduces friction between moving parts to prolong their lifespan and extend their lifespan.
Silver’s durability makes it an excellent material choice for products designed to withstand tough environments, like medical devices. Silver can be used to plate medical devices like insulin pumps and stethoscopes due to its antibacterial properties – this sterile quality is particularly crucial in environments that prioritize hygiene such as hospitals.
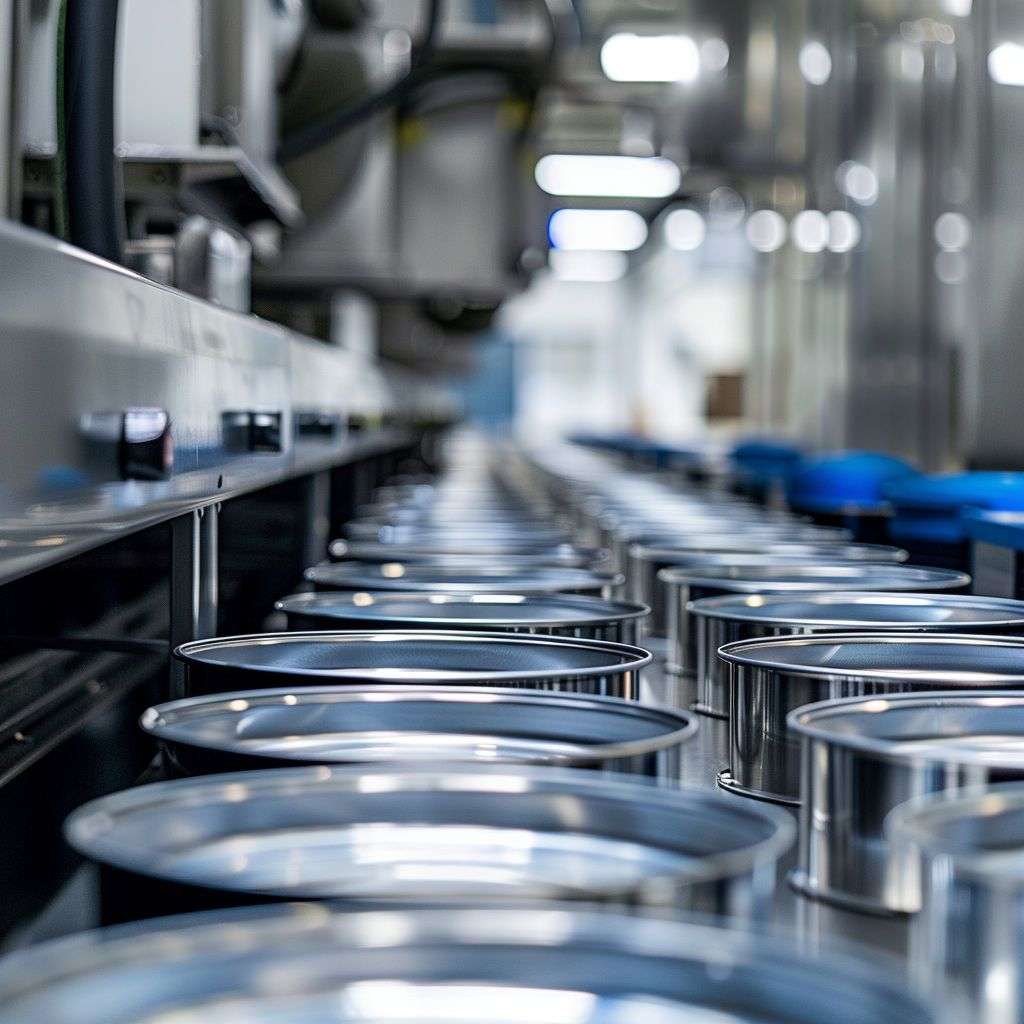
Even with its strong corrosion resistance, silver remains vulnerable to oxidation when exposed to sulfur-containing materials, leading to the process known as sulfidation and eventually corrosion. Therefore, it is imperative that after plating has occurred an additional anti-tarnish treatment be applied post-plating in areas with high sulfur concentration in order to ensure proper performance of your product.
Electroplating involves immersing a substrate metal in an electrically charged solution of silver ions that when activated will deposit onto it to cover it with your chosen metal-in this case, silver. Because silver is such an adaptable metal, you can alter its hue depending on your product needs and achieve matte, dull or bright finishes for both smooth and textured surfaces.
silver has an outstanding corrosion resistance; however, its susceptibility to tarnishing when exposed to sulfur-containing materials should be addressed with precaution. Therefore, using an additional tarnish inhibitor and storing your products in sealed bags with desiccates and silver saver paper will eliminate any chance of your products tarnishing during storage or shipment.
Due to the cost and complexity of plating processes, it’s vital that you choose an ideal silver coating thickness for your application. A Square engineer can recommend an ideal thickness based on factors like environmental conditions, base material type and desired electrical/thermal conductivity levels for your project. Taking this into consideration can save costly errors during manufacturing while guaranteeing your product arrives functional and long lasting at its destination.
Durability
Silver is an extremely durable metal that can be utilized across many different industries and applications. It stands up well to heat and corrosion better than many other plating options such as gold or palladium plating options, making it the ideal solution for high temperature environments such as electronics manufacturing or automotive assembly lines. Silver also boasts great lubricity properties that reduce failure risk in such settings.
Due to its durability and conductivity, silver has long been considered the go-to plating material for various metal finishing applications. For instance, electrical component manufacturers frequently turn to silver plating because its superior conductive properties make soldering simpler than with other metals; making silver the material of choice among aerospace engineers, electronics manufacturers, and car manufacturers alike.
Silver plating’s high durability enables manufacturers to produce parts with longer lifespans than their unplated counterparts. This can save companies money in the long run while increasing profit margins; additionally, complying with environmental regulations and meeting industry standards may be achieved more easily.
For maximum longevity of a silver-plated product, it is crucial to follow proper maintenance guidelines. This involves regularly clearing away debris and cleaning the part; additionally it is suggested using non-sulfuric coatings which prevent tarnishing. Furthermore, prior to electroplating any product it should be inspected to determine its suitability for electroplating and perform any necessary pre-treatments if required.
Careful maintenance will allow a silver-plated product to retain its attractive appearance for many years, resisting tarnishing and rusting as well as polishing to restore its luster. Silver is considered a noble metal, meaning it resists corrosion more efficiently than most precious metals.
Silver may be hardy metal, but it still can be susceptible to corrosion if exposed to certain chemicals and substances. To maintain optimal condition for silver-plated products, avoid sulfur exposure as this substance tarnishes metal over time. Furthermore, using non-sulfur sealers when packaging finished goods is recommended.
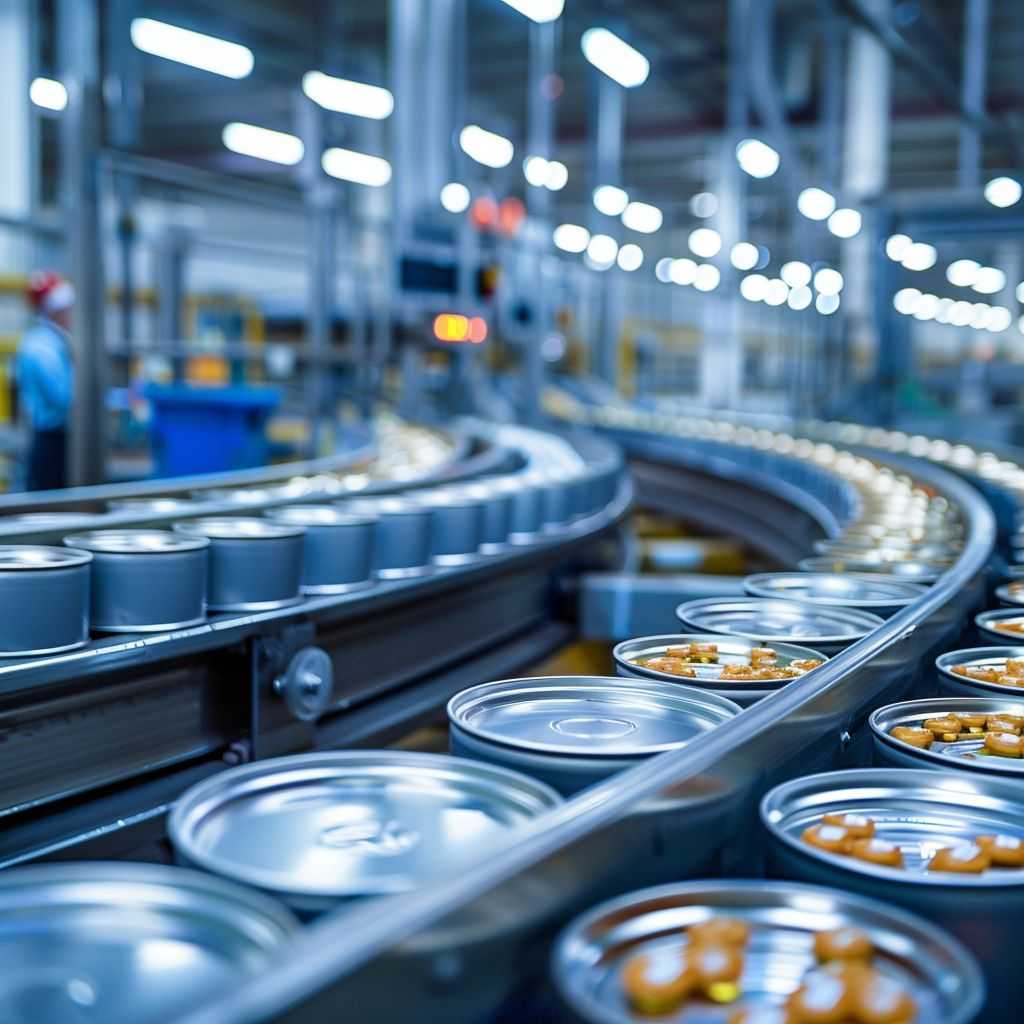
Appearance
Silver plating provides a beautiful shiny finish, making it ideal for products requiring high reflectivity such as laser equipment. Silver’s incredible durability also makes it long-term resistant to corrosion; furthermore, solderability makes it popular across industries; however, due to rising commodity prices the cost of plating every product with silver has become cost prohibitive and uneconomical.
There are alternative plating solutions to silver that will still produce beautiful finishes, such as tin plating. Tin is often chosen over silver because it is cheaper, more durable and offers similar levels of reflectivity; however, its primary downsides include poor conductivity and melting at lower temperatures than its silver counterpart.
Tin’s ability to bond with other metals makes it ideal for wire and cable manufacturing applications, such as New England Wire Technologies’ in-house plating options such as tin and silver plating – our experts can assist in selecting the ideal one for you!
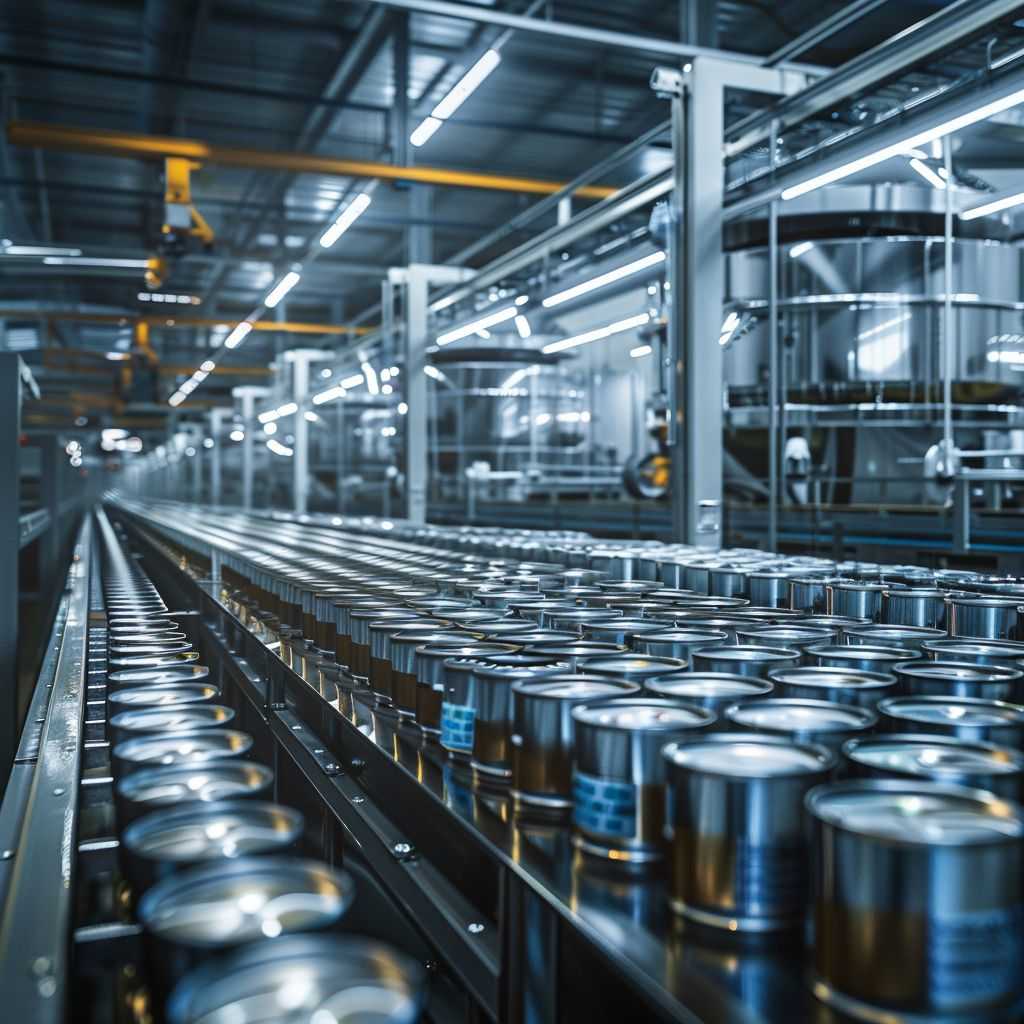
Silver is one of the world’s most-utilized precious metals, making it ideal for medical applications due to its biocompatibility and inherent resistance to bacteria. Furthermore, it’s extremely ductile so can easily conform to any host substrate shape while being anti-galling, lubricious, and corrosion resistant – qualities which also make silver an essential choice in other industries.
When choosing a silver electroplating service, make sure that they have both experience and knowledge to complete your project correctly. A quality provider will use cutting-edge methods and fixtures to selectively plate only those parts which absolutely need silver plating; saving both time and money while meeting all required standards for their product.
Experienced silver plating services will understand how to tailor products for use in harsh aerospace environments and can identify potential issues before they become costly issues, offering solutions and providing recommendations on how best to overcome them.