Printed Tinplate: Durable, Customizable, and Eco-Friendly Packaging Solution
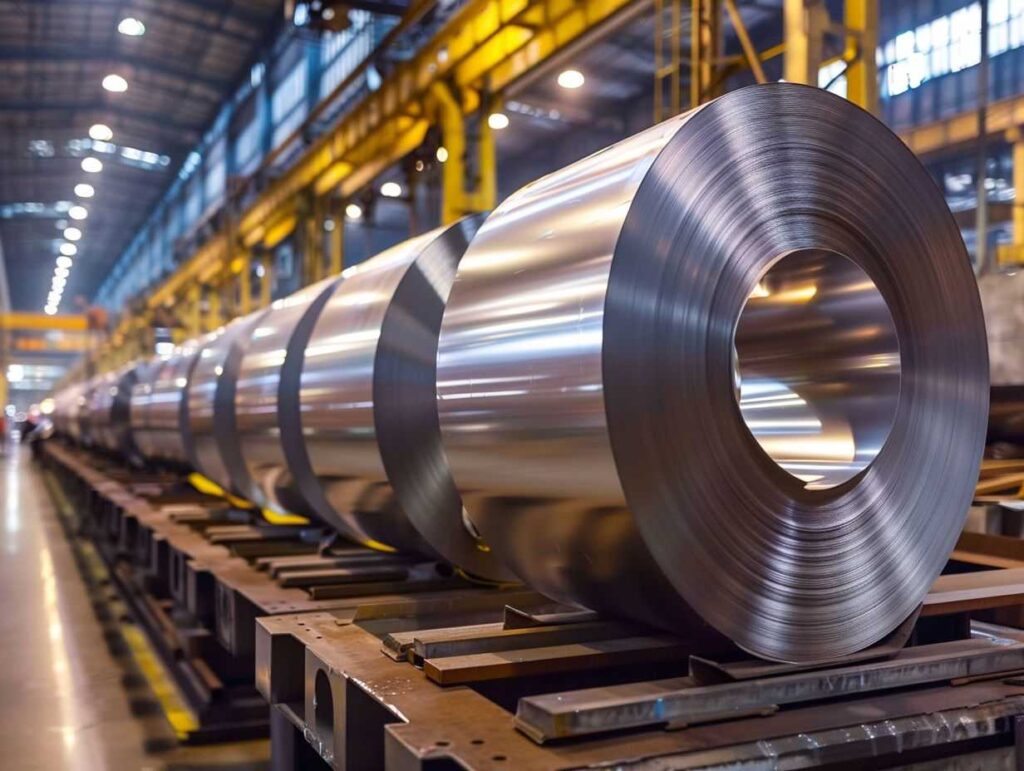
Printed Tinplate Packaging Corrosion Resistance
Printed Tinplate packaging is a form of metal packaging created by applying custom designs directly onto its tin-coated steel surface. This highly durable packaging material exhibits excellent corrosion resistance, making it suitable for packaging food, toys, decorative tins and more. Catering to individual customer requirements, it comes in various sizes, thicknesses, and colors – something printed tinplate can provide.
Conventional tinplate is typically composed of low carbon steel that has been electrolytically coated with a thin layer of tin using electroplating technology. The amount of tin coating accounts for less than 1 percent of total plate thickness; its gauge range is 0.13 to 0.50 mm and it may feature either smooth or embossed surfaces. Typically, this aspect of its construction remains intact to preserve its original aesthetic qualities.
Tinplate packaging material is an exceptional, safe food-grade packaging material for food items, offering good corrosion resistance and suitable storage of canned products. Tinplate also boasts an appealing metallic luster which makes painting and printing simple, making this versatile packaging material suitable for many products and purposes. Available in clear/transparent, white, buff colors, as well as lacquer finishes which protect it against scratches, rusting, or other forms of damage, it provides ideal conditions for product packaging in its various forms.
Tinplate offers durability and corrosion resistance as well as formability and strength, making it suitable for many different applications, including:
- Cans for food and beverages
- Aerosol containers
- Decorative tins
- Other industrial settings
Electrolytic printed tinplate, unlike standard tinplate which features a smooth finish, offers greater design freedom to manufacturers, enabling them to create visually appealing packaging with greater design flexibility. Furthermore, electrolytic printed tinplate can also be formed into various shapes for easier recycling purposes.
Printed tinplate cans are an ideal packaging choice for beverages and canned goods, providing protection from:
- Moisture
- Oxygen
- Durability
- Recyclable materials
- Easily formed shapes making it cost-effective.
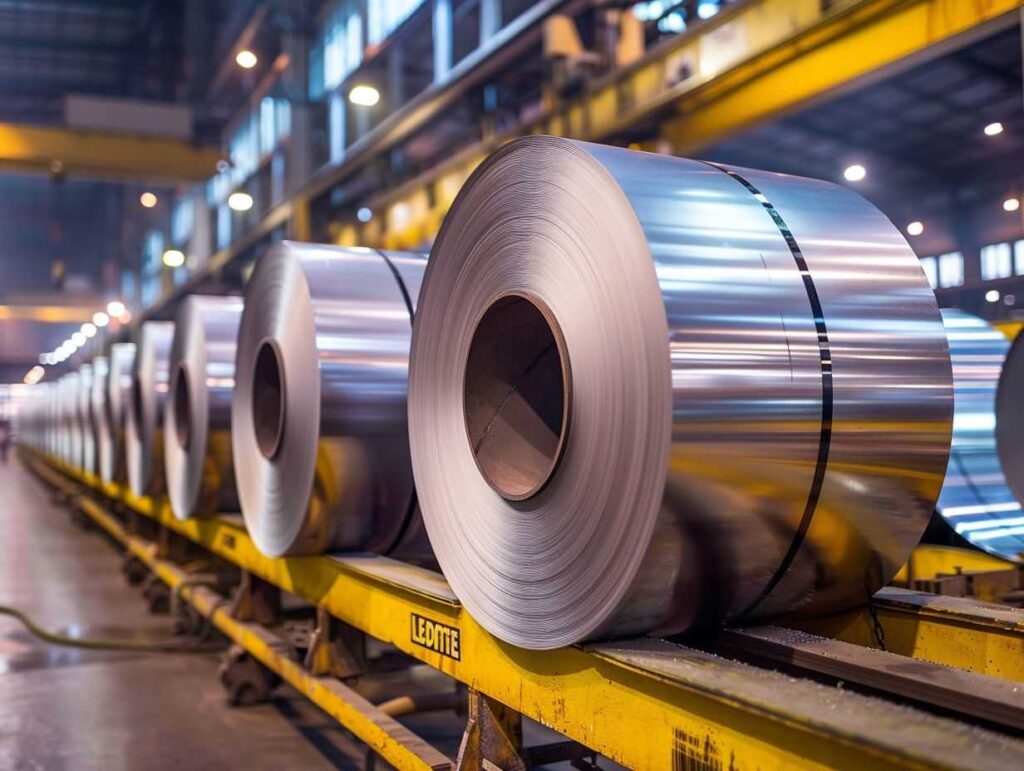
Non-Toxic
Printed tinplate is non-toxic, making it suitable for food packaging. Not only that, but its eco-friendliness and biodegradability also makes it attractive to environmentally conscious customers. Furthermore, its smooth surface allows for high-resolution printing capabilities; it can be formed into different shapes and sizes without deforming. Finally, its moisture and corrosion resistance makes printed tinplate an attractive choice for cans and other containers.
Printed tinplate sheets feature attractive designs and lightweight construction for easy handling and craftability, making these products suitable for crafting jewelry, art projects, and more. There is also an assortment of colors and styles available to satisfy every taste; electrolytically produced products offer longer durability.
Tinplate is a type of metal coated in tin to prevent corrosion. Originally, its backing metal was wrought iron; today, most commonly cold-rolled steel is used as its backing material. Tinplating protects steel against corrosion while improving its mechanical properties, such as resistance to bending resistance. Furthermore, this bright finish can be lacquered or printed upon for lacquer or printing applications and comes in various thicknesses for customization purposes.
- Conductivity of this ink measures 1000 S m-1 while sheet resistance stands at 15 O sq-1. Furthermore, its moisture stability remains steady, enabling stencil printing. Graphite flakes offer numerous electrical contacts and shear-thinning gel properties which contribute to its ability to withstand shear stress.
Printed tinplate sheets offer excellent corrosion and rust protection, making them the ideal material to create containers for food, beverages, aerosols, and chemicals. In addition, printed tinplate sheets make excellent toys and decorative tins; lacquered in gold hues provide eye-catching contrast. Laser cutting into custom shapes is possible to customize each project to personal needs and welded quickly with minimal effort required.
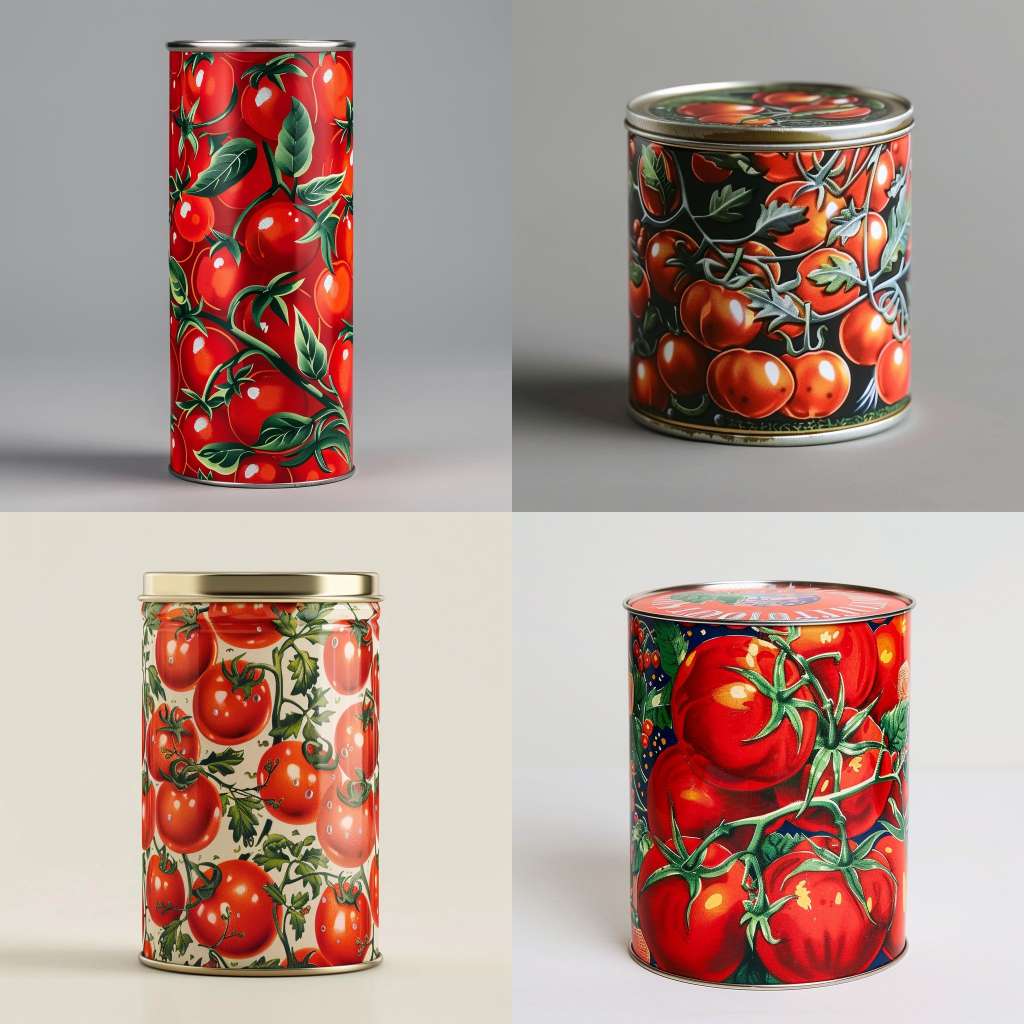
Strong Pattern
Printed tinplate sheet has a stunning metallic sheen that makes it perfect for food packaging applications. In addition, its durability, corrosion resistance, and solderability make it the ideal material. Not only can cans be created from it; other containers may also benefit from using printed tinplate sheets; non-toxic finishes make this safe to use with food containers as well. Its strong pattern resists denting and scratches. Plus, its lightweight nature makes crafting easier!
Tinplate first emerged as a food packaging material during the 1800s and remains an integral component of modern society today. Used to package:
- Foods
- Beverages
- Chemicals
- Paints
- Spray cans
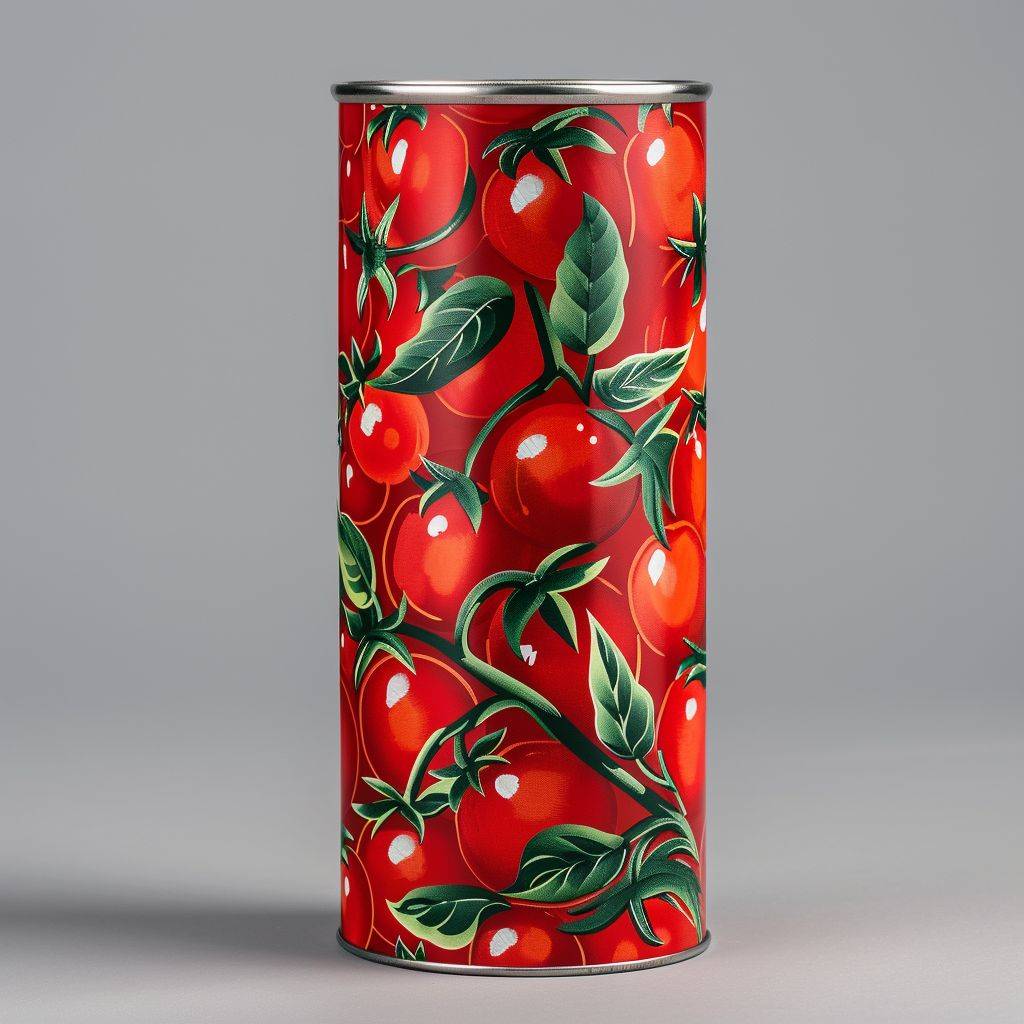
To produce high-quality and long-term prints on tinplate, the proper ink must be chosen, including one with strong desiccation properties, high adhesion ratings, and vibrant color display characteristics that can withstand high heat-processing temperatures without cracking under pressure.
Tinplate printing differs significantly from paper. Due to the hard and thick nature of tinplate, ink struggles to adhere to its surface; therefore, a thin coat of coating (usually composed of iron-tin alloy and chromium oxide) is applied before printing commences in order to protect it from rusting and ensure its adhesion to metal surfaces.
Printing on tinplate is typically accomplished using offset printing; however, due to its hard and ink-repellant surface, its results tend to be less clear than on paper. Furthermore, its hard surface causes dots to deform during printing, which results in deeper midtone jump levels with sharper transitions between them.
Tinplate is manufactured using a combination of steelmaking and finishing processes, starting with milled, wrought iron or low-cost milled steel as its base metal. Once coated with tin plating to prevent further rusting, tinplate can then be ready for use.
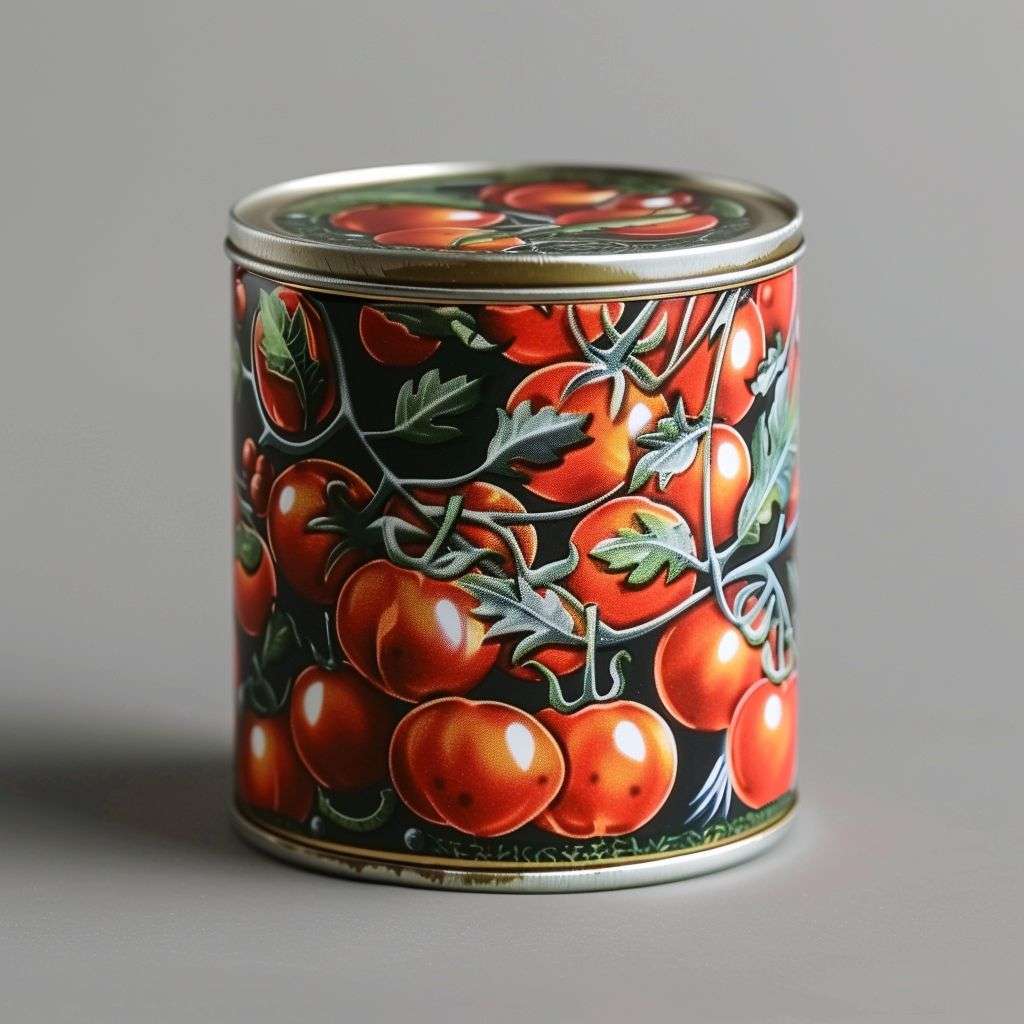
Moisture Resistance in Printed Tinplate
Moisture resistance of printed tinplate is a critical element of its quality. As this material is intended for use in cans and other containers, its moisture resistance must stand up against bending, stretching, welding, flanging, sealing, and other processes required in the production of the final product. In addition, its resistance must withstand chemicals used during production such as hydrochloric and nitric acids as well as exposure to moisture, which could corrode its protective tin coating surface and compromise its integrity.
Tinplate is a thin steel sheet coated with tin to give it its beautiful metallic luster and superior corrosion resistance, solderability, and weldability properties. Common uses for it include:
- Food containers
- Gaskets
- Seals
- Automotive air and oil filters
- Baking pans
- Graters
- Badges
- Toys
Recently, it has even been given laminated plastic coating for interesting textural effects.
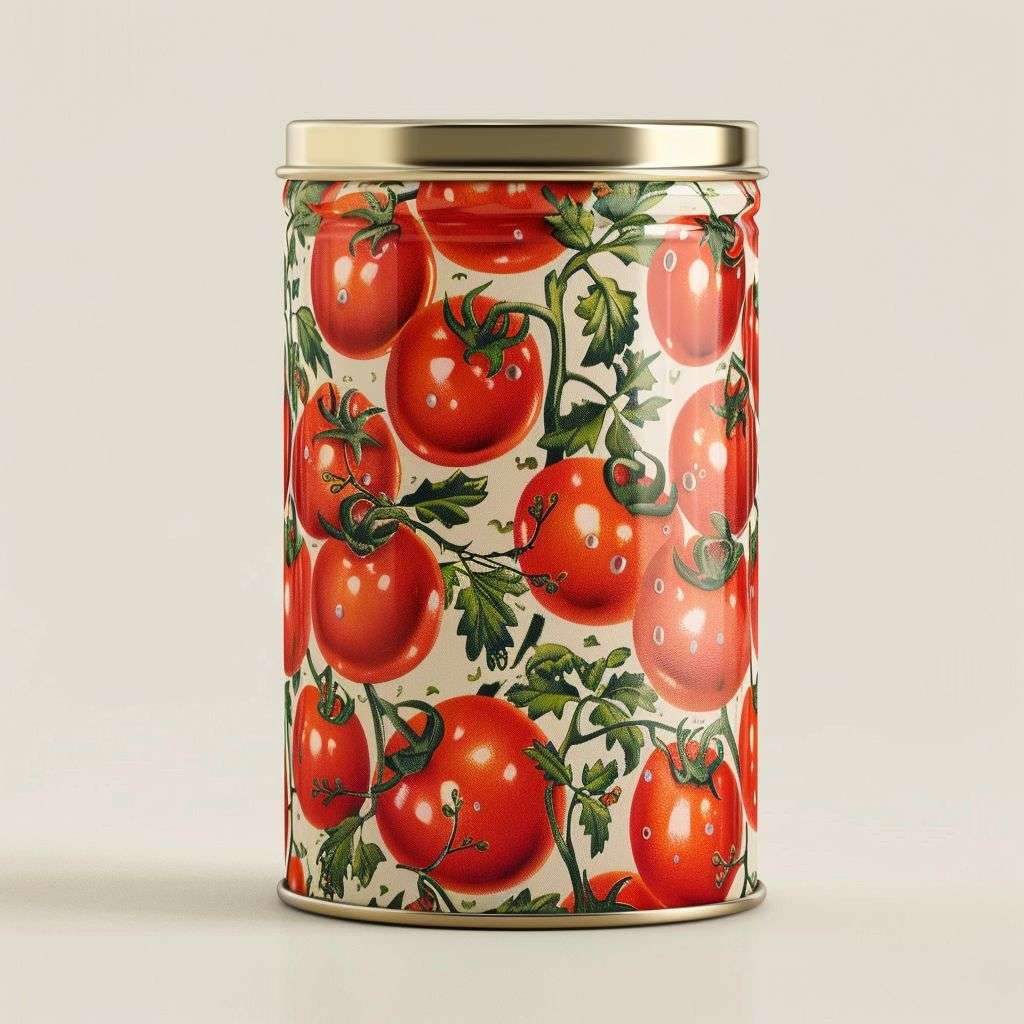
Printed tinplate is available in numerous sizes and thicknesses to meet various uses. The printing process takes place after coating has occurred, using special inks with high adhesion properties for printing. These inks must also possess water resistance to avoid discoloration, leaks, or tears in the process.
Recent research examined the conductivity of inkjet-printed Ag- structures printed with inkjet printers on two commercially available, uncoated paper substrates. Results demonstrated that their conductivity depended largely on the roughness and porosity of the substrate, with smooth surfaces having higher conductivity levels than rough ones. However, their conductivity can decrease substantially under physical and chemical treatment due to inks used for printing deposition inhibiting its formation. Moreover, physical treatments could absorb printing inks used for printing/deposition, thus inhibiting formation altogether.
Get Your Quote Now
Related Posts
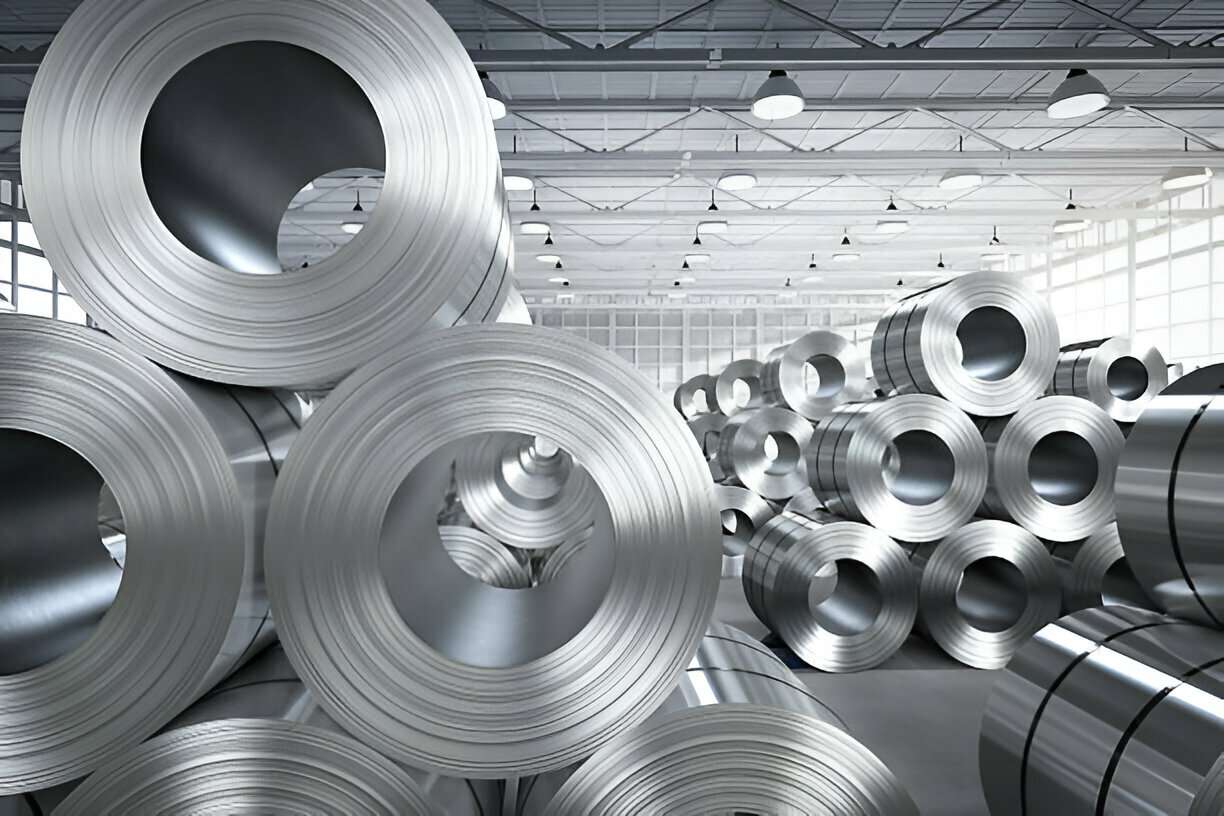
Is it Safe to Cook in Tin-Lined Copper Pots?
Copper heats quickly and evenly (even better than stainless steel! ), helping you conserve energy by
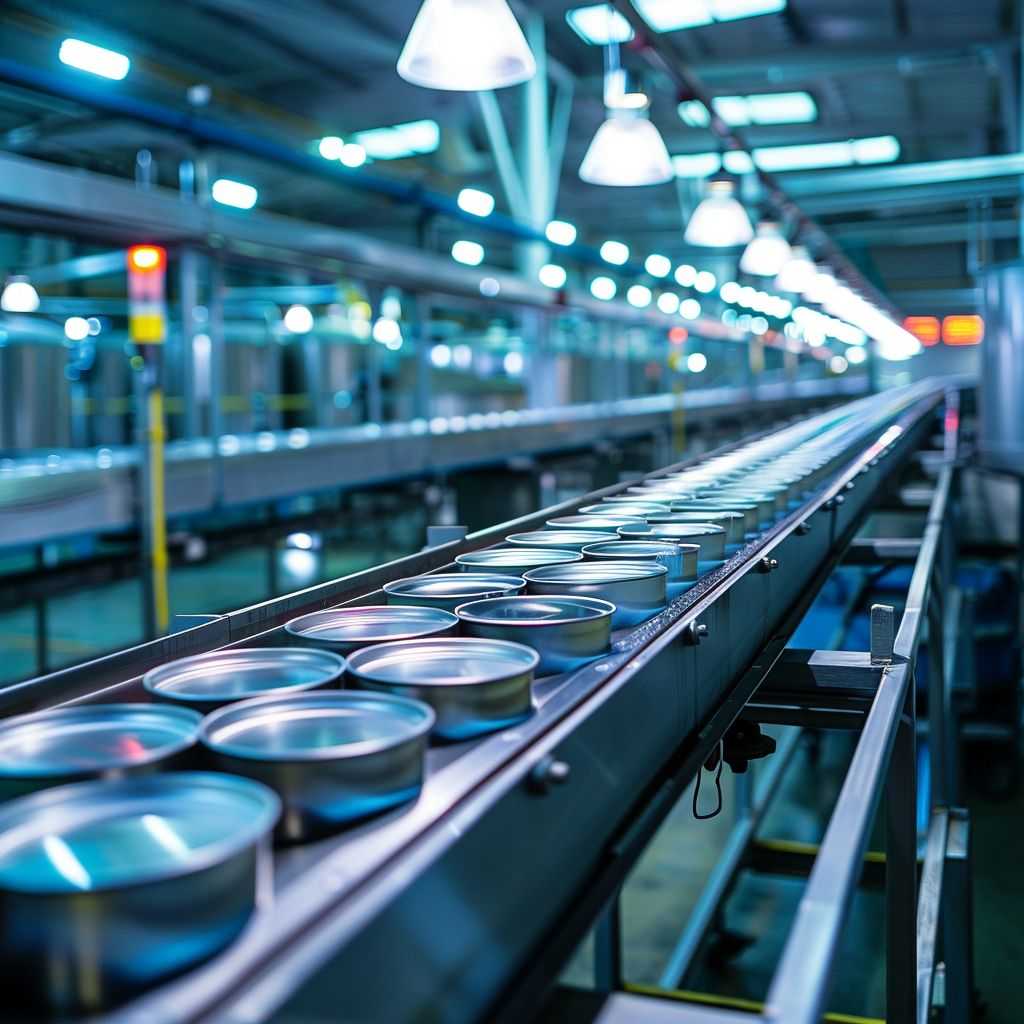
Is Silver Plating Better Than Tin?
Silver has long been used in multiple industries, from healthcare and consumer to electronics, automotive and