Tin plating protects copper from degradation in humid or marine environments, increasing longevity and optimizing performance.
Tinned copper is easy to solder, making it the perfect material for applications requiring secure connections between components or wires. Furthermore, its tin coating offers excellent thermal and electrical conductivity properties.
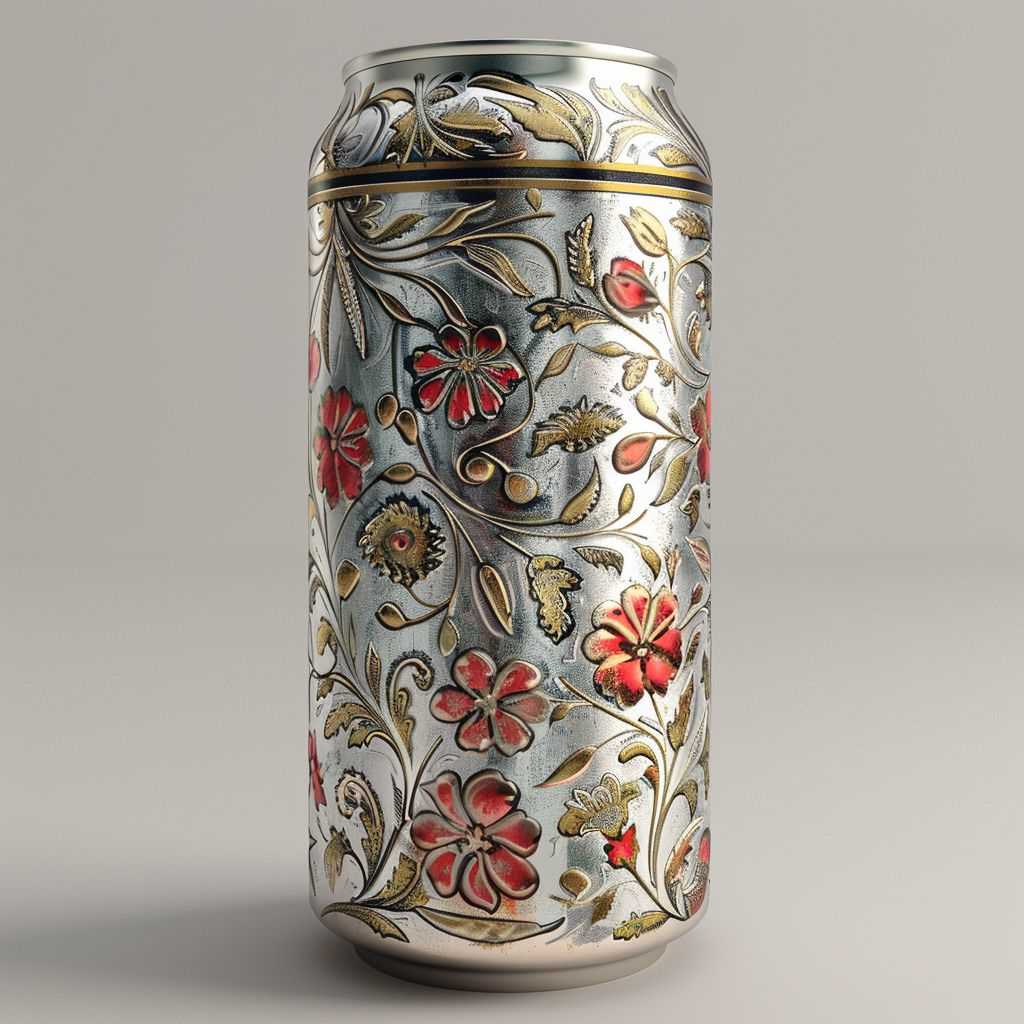
1. Corrosion Resistance
Tin plating is an increasingly popular technique applied to copper products like bus bars used to pass current in electronics and power devices. Tin plating protects copper against environmental factors like moisture, humidity and salt spray which could otherwise erode away its conductivity, leading to its loss altogether. Tinned copper also allows easier soldering than its uncoated counterpart as its porous surface acts as an excellent receptacle for solder.
Copper alloys such as bronze, brass and silver are vulnerable to corrosion and tarnish due to their narrow operating temperature windows and high melting points, but Tin is an ideal plating material as its melting point is lower than silver and operating window wider. Furthermore, Tin is highly resistant to oxidation and tarnish as well as many chemical agents such as mineral acids like sulfuric acid – making tin/lead plating popular for lead acid battery applications.
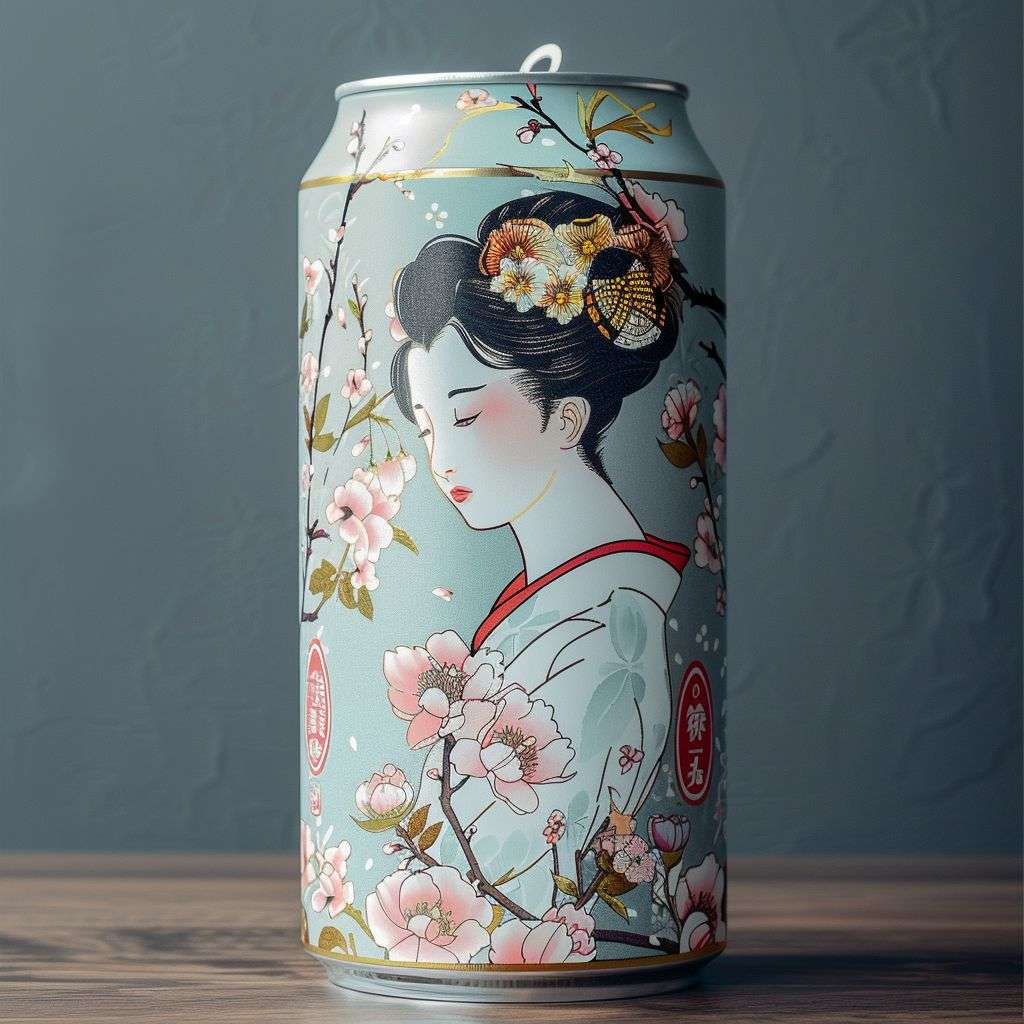
Tin applied to copper forms an intermetallic layer between them that has lower conductivity than either metal alone but higher conductivity than its bare copper substrate – thus explaining why tinned copper has greater conductivity than uncoated copper.
Tin coating protects copper wire from corrosion and extends its lifespan by adding conductivity. Bare copper wire corrodes rapidly in humid or rainy environments, hot temperatures and certain soil types; this corrosive damage disrupts impedance circuits and causes malfunction. A tin coating keeps copper protected from rust for extended longevity and safer usage.
Tin can be applied to copper by immersing it in molten tin – known as commercial hot dipped tin (HDTc), electrolytic, or plating processes; mechanical rubbing or air jet wiping will leave it mechanically matte tin; otherwise known as air leveled tin (ALT). Tin may also be combined with other metals such as nickel and silver for special applications such as lead/acid battery contacts – finding the appropriate metal can impact performance, durability and safety of any project!
Choosing the correct metal can have dramatic impacts on performance, durability and safety of any project; selecting it will have long term impacts that will directly influence performance, durability, safety or performance of any project! Choosing the appropriate metal can have drastic impacts on performance, durability and safety – choosing your application accordingly will impact performance, durability and safety!
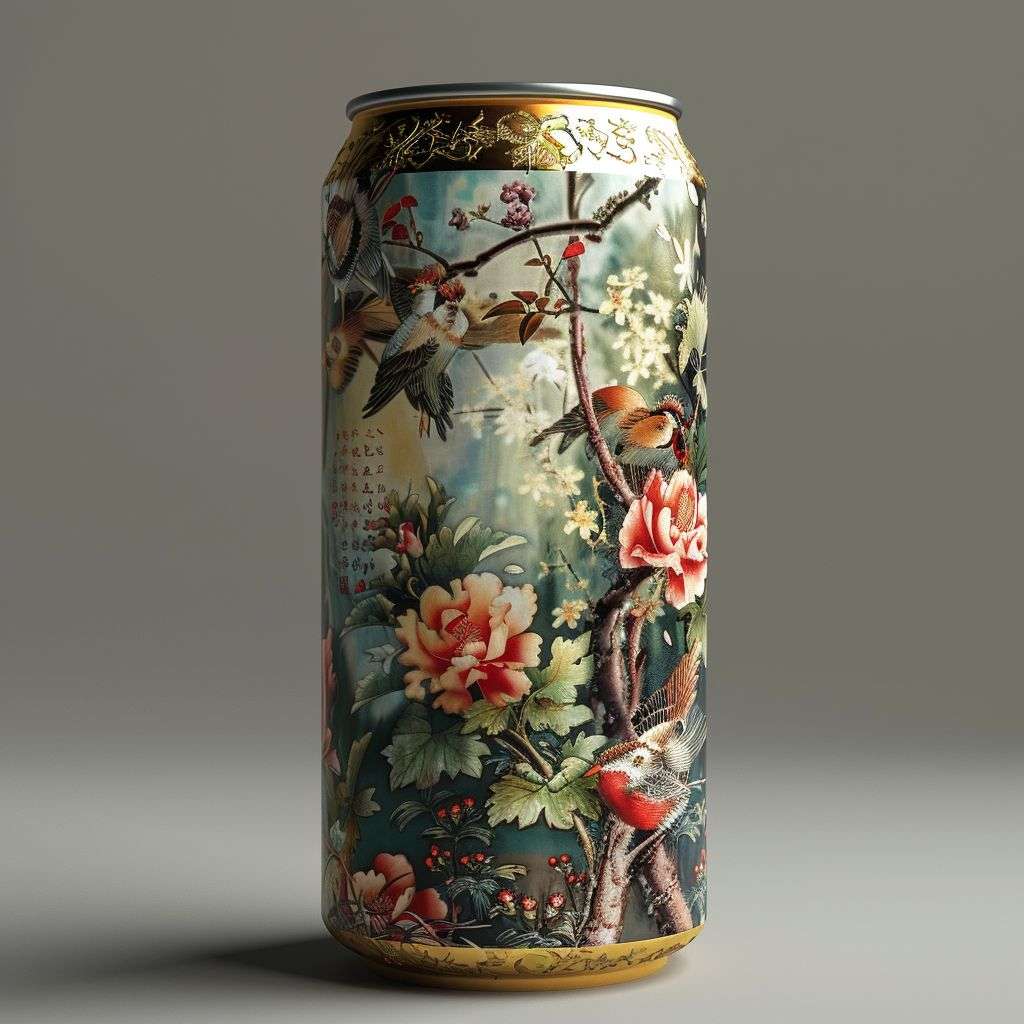
2. Solderability
copper wiring can be enhanced for solderability with nickel plating that includes gold, silver, tin or tin/lead plating in order to enhance solderability and conductivity by plating it with nickel, gold, silver, tin or tin/lead platings such as nickel/gold/silver/tin platings like gold/silver. This makes connecting components much simpler while increasing conductivity compared to bare copper wiring – although nickel tends to oxidize over time which interferes with soldering processes and cause problems in end products; Tin plating prevents this oxidization process making soldering much simpler compared with its nickel counterpart over time and creating issues in your end products whereas its nickel counterpart may oxidize over time which interferes with soldering processes causing issues in your end products whereas nickel can oxidize over time which interferes with soldering processes making soldering much simpler!
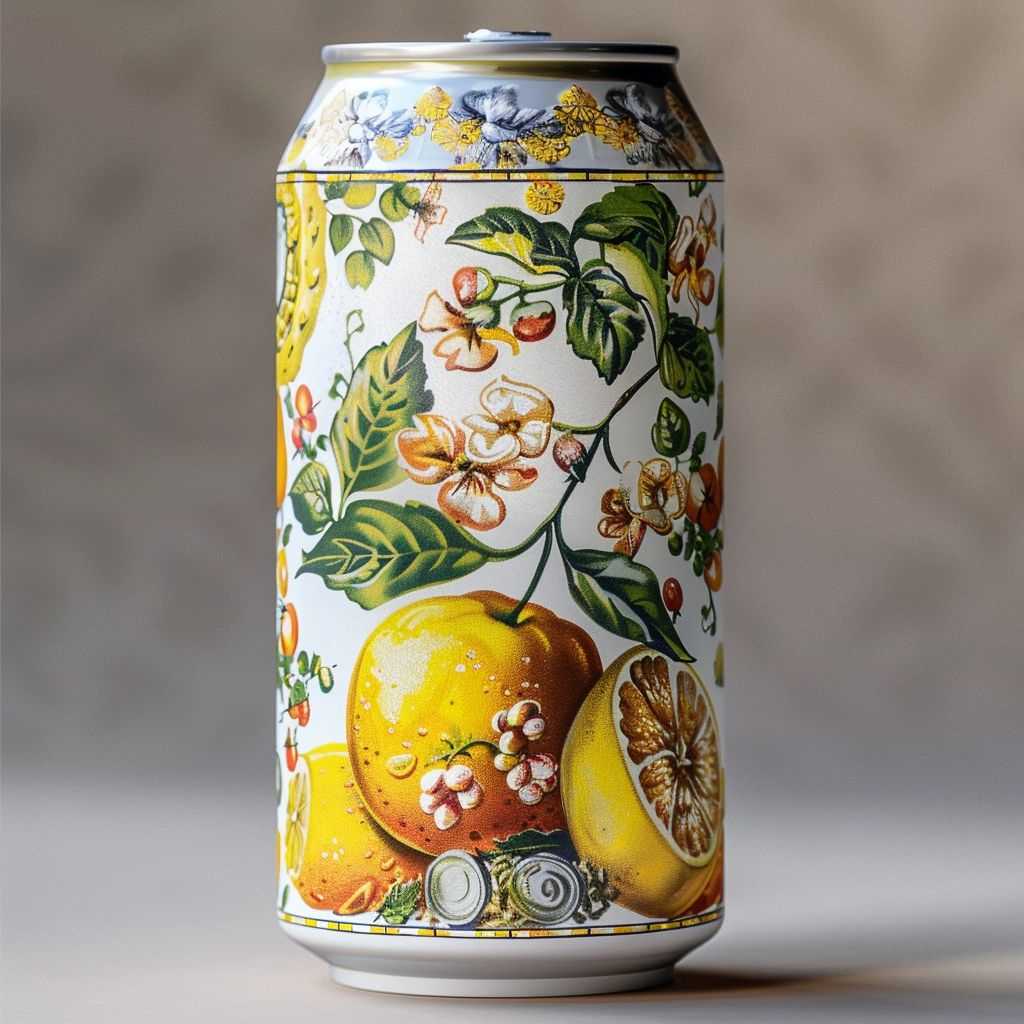
Tin is an effective corrosion and chemical attack barrier, helping your wires last longer while improving reliability in the electrical industry. This feature is particularly significant when used on high-voltage cables which carry high energy currents; busbars in power systems or breaker panels often employ this protective surface to shield their copper foundation and extend their service lives while increasing reliability.
Tin/lead plating is an ideal combination of corrosion resistance and solderability for electrical applications, providing an optimal combination between these attributes. The alloy can be tailored according to your specifications; typically this comprises 5/95 (55% tin, 95% lead) or 95/5 (95% tin, 5% lead) coatings which ensure the coating can withstand even the harshest electrical and mechanical stress while still offering excellent solderability.
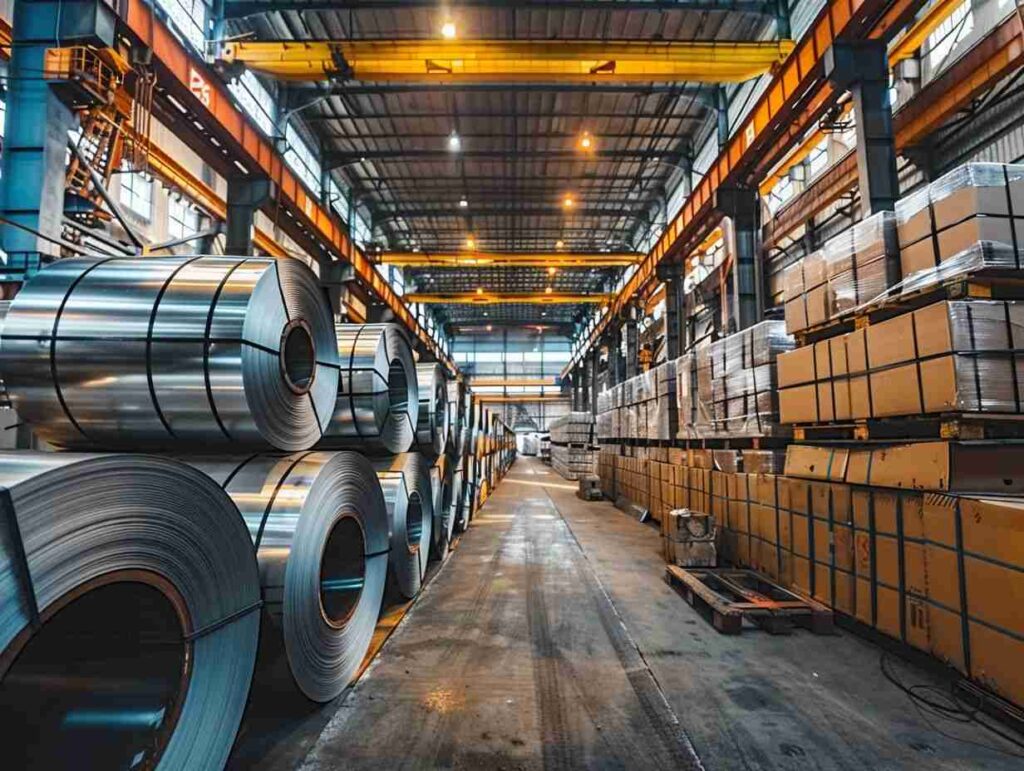
Although poor solderability on tin-plated copper may occur occasionally, when using an appropriate thickness of tin. To achieve optimal results, select a tin/lead coating with at least 0.002um thickness for long solderable life and low contact angles between molten solder and its surface.
Darkening of tin plate is a common issue, caused by its oxidization and subsequent loss of solderability, usually from exposure to UV light, excessive humidity or prolonged storage prior to soldering. When this happens it is recommended to replate with alkaline etching in order to remove any tin oxide build up and restore solderability of your tin plated copper; alternatively you could simply apply an appropriate flux and resolder in order to correct the problem – either approach will usually resolve this issue and return it back into good solderability!
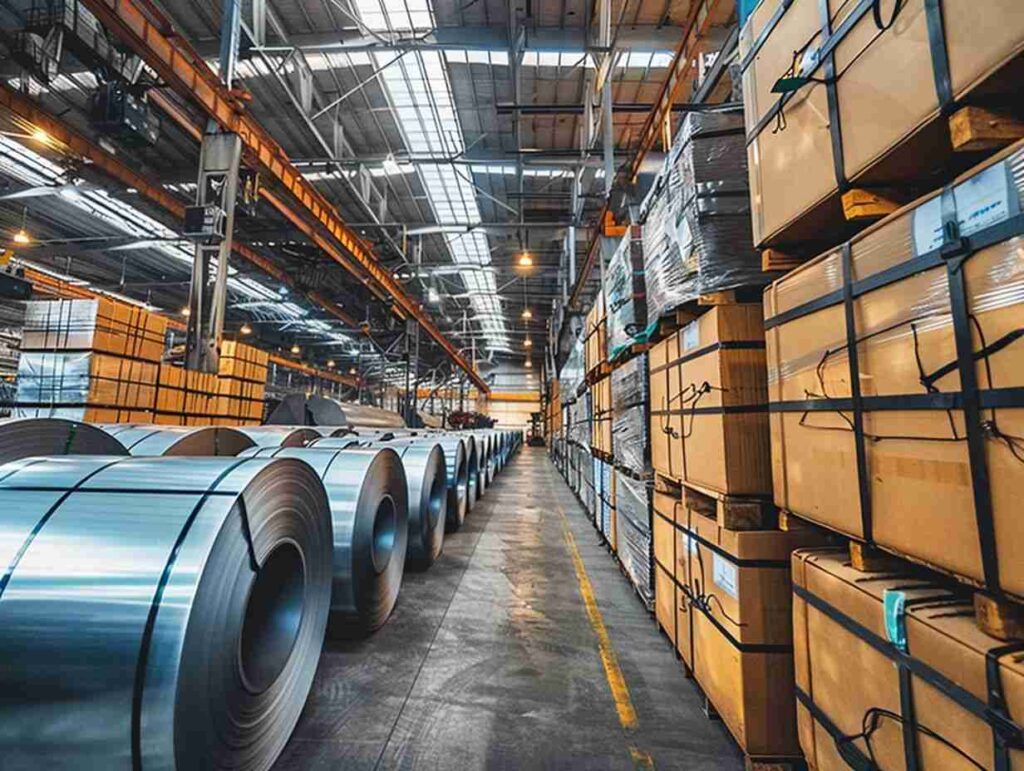
3. Aesthetics
Tin is an economical metal that can be used for plating applications at lower costs than gold or silver plating, providing excellent corrosion resistance, solderability, lusterous appearance and eye-catching appeal; making it popular choice in jewelry applications and decorative applications such as decorations. Furthermore, its ductility allows it to create complex curved or bent metal parts.
Tin-coated copper parts can often be seen in various industries. Common applications for them include electronics, mechatronics, hardware, construction and fasteners as well as manufacturing food equipment and solar panels.
Tin plated copper must fulfill the needs of its application in terms of both wear and tear resistance, corrosion protection and electrical current resistance. A plating specialist can advise you as to which thickness of tin plating best meets these specifications for your project. Wear and tear will determine which tin plating thickness you use based on wear patterns as well as corrosion or electrical current resistance requirements.
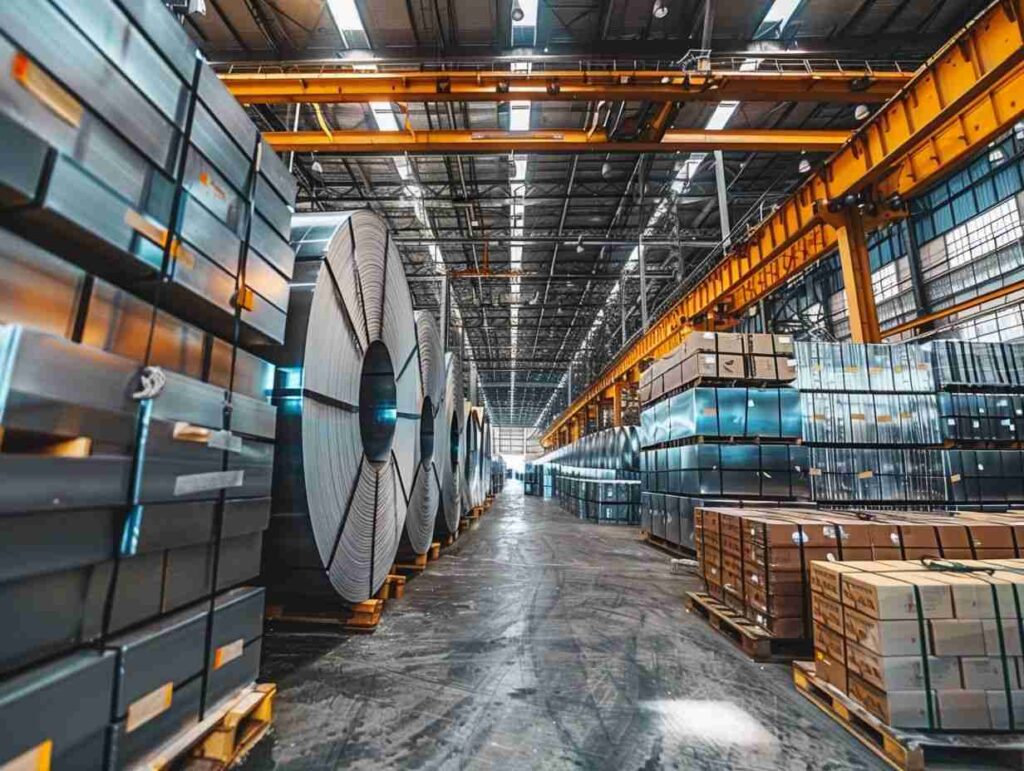
Tin plating thickness typically ranges between 2-5 microns. Depending on your industry and application, you may require thinner or thicker plating layers; for example, copper bus bars need to meet certain conductivity standards while still offering adequate corrosion resistance.
Consideration must also be given to the type of tin alloy used during electroplating. Common alloys for use include nickel, cobalt, lead, silver and zinc; each alloy serves its own specific purpose when added to plating processes such as hardness reduction or increasing ductility – nickel and cobalt are often added for hardness reduction while silver increases ductility while zinc offers solderability enhancement and corrosion protection.
Before coating any part with tin, it must first be thoroughly cleaned to eliminate any oil or contaminants, to achieve optimal results and limit intermetallic migration risks that could damage it. Next, baking should take place so as to prevent hydrogen formation that could compromise later quality of tin plating application.
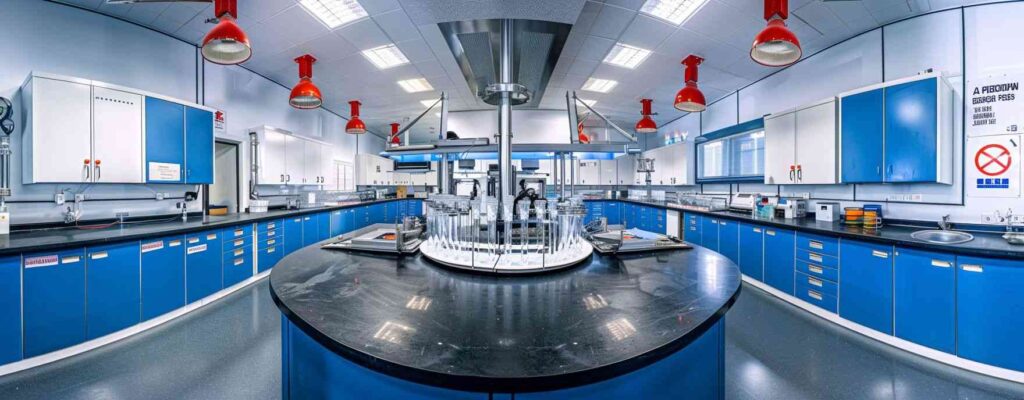
4. Safety
Copper is an integral component of many electrical and electronic devices, serving to transport current as well as mount components and dissipate heat in various applications. Copper bus bars – large conductors made of copper used to carry current through power distribution systems, electronic devices, automotive vehicles, etc – play an integral part in many power distribution systems as well as electronic devices; typically coated in tin to improve durability and protect from corrosion.
Bare copper can become vulnerable to oxidation over time, which can severely diminish its performance and become unsafe. Tinned copper, on the other hand, is less vulnerable to this process and more stable in various environments; that’s why tinned copper is commonly employed for projects where prolonged moisture exposure will occur such as underground railways or marine and underwater applications.
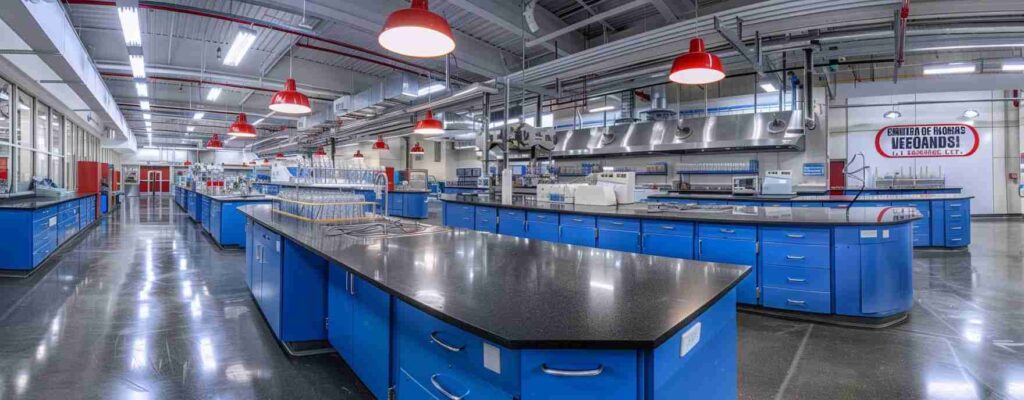
Tinned copper wire has superior salt spray resistance than its uncoated counterpart, making it suitable for marine and other saltwater-exposed applications. Tin protects copper from corrosion by creating an intermetallic shield layer, while bare copper may be susceptible to interactions that cause it to corrode more quickly due to interactions with other metals and corrosion-prone elements in its surroundings.
An intermetallic layer composed of tin and copper protects copper against acid contamination that could damage electrical wiring systems. Since tin has a lower melting point than acid, tin will not melt copper and cause it to corrode as quickly.
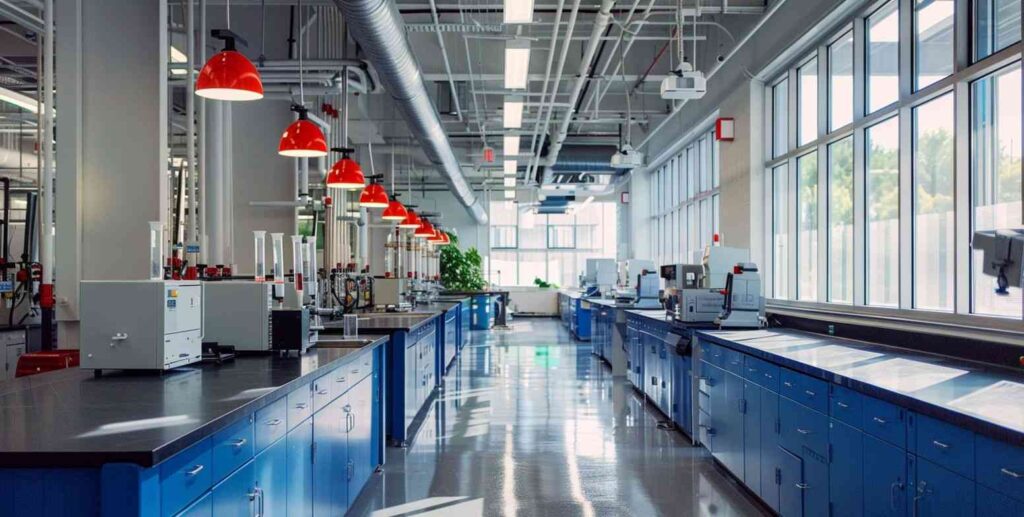
Although tin-plated copper offers many safety advantages, it may not always be suitable. For instance, it has a lower temperature operating window than unplated copper and can form conductive growths known as whiskers or dendrites due to stresses within the plating process or external forces like bending or stretching.
However, inorganic tin compounds enter and leave your body quickly when breathed in or consumed through food or drinks. Even when eating canned goods such as tuna, very little inorganic tin enters your bloodstream; most leaves through digestion within 24 hours in your feces.